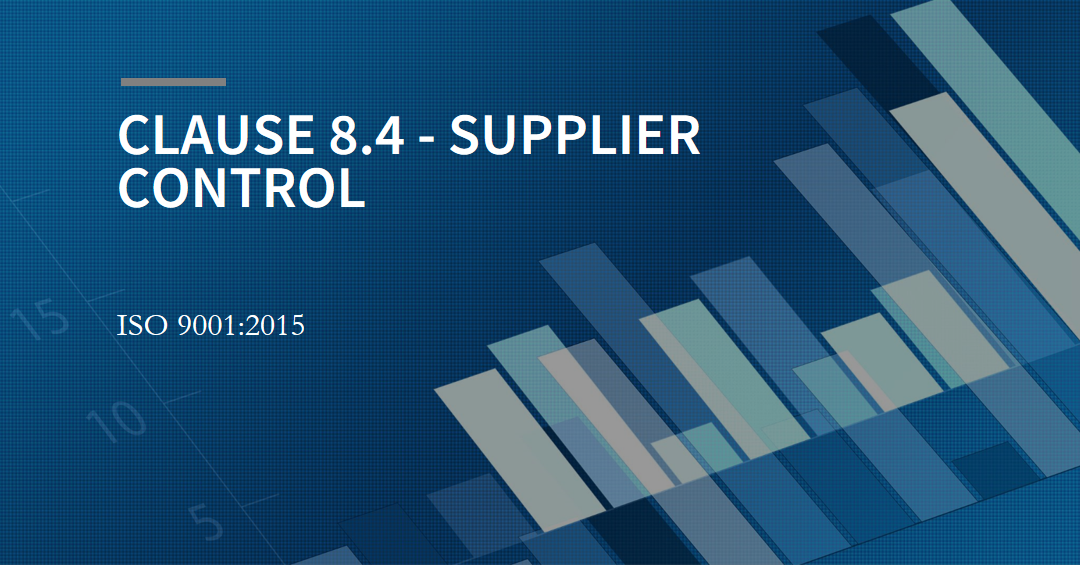
Introduction
Welcome to our in-depth exploration of Clause 8.4 - Supplier Control in ISO 9001:2015. This key component of the ISO 9001 quality management system (QMS) standard focuses on the crucial aspect of managing external providers to ensure that the quality of your final product or service meets the highest standards.
In this blog post, we'll delve into the specifics of what Clause 8.4 entails, why it's so important, and how to implement these standards effectively within your business. Whether you're a seasoned quality manager or new to the ISO 9001 framework, understanding and mastering supplier control can significantly impact your business's success and your customers' satisfaction.
ISO 9001:2015 is an internationally recognized standard that sets out the criteria for a quality management system. It helps businesses and organizations be more efficient and improve customer satisfaction. A crucial part of this standard is Clause 8.4, which deals with the control of externally provided processes, products, and services. It ensures that anything that comes from outside the organization meets your own quality requirements.
Let's begin our journey through Clause 8.4 and unravel how to effectively control suppliers to elevate the quality of your operations.
What is Clause 8.4 - Supplier Control?
Clause 8.4 of ISO 9001:2015, titled "Control of externally provided processes, products, and services," is a comprehensive section dedicated to ensuring that any external inputs into your business's products or services meet your quality criteria just as reliably as those produced internally.
The essence of this clause is the concept of extending your quality management system's reach beyond your immediate operations to encompass your suppliers and vendors. It acknowledges that the quality of your outputs is deeply intertwined with the quality of inputs received from external sources. To maintain consistency and reliability in your final offerings, it's imperative to have a robust system for controlling these external influences.
Key Objectives of Clause 8.4:
- Ensure Compliance: External providers' processes, products, and services must conform to specified requirements.
- Mitigate Risks: Identify and control any potential risks to your product or service quality that may arise from external sources.
- Promote Consistency: Achieve consistency in the quality of products or services by managing the variability of external inputs.
- Enhance Customer Satisfaction: Ultimately, supplier control aims to protect and improve customer satisfaction by consistently meeting customer requirements.
By adhering to this clause, organizations demonstrate their commitment to quality and their ability to manage the entire supply chain effectively. This, in turn, builds trust with customers and stakeholders, proving that the organization is a reliable link in the chain of supply.
In the following sections, we'll break down the individual components of Clause 8.4 to provide a clear road map for implementing effective supplier control.
Breaking Down Clause 8.4 - Supplier Control
Clause 8.4 of ISO 9001:2015 can be further dissected into three sub-clauses, each addressing different aspects of supplier control. Understanding these subdivisions allows for a more systematic approach to managing external providers.
8.4.1 General Requirements: Establishing the Foundation
The general requirements in clause 8.4.1 establish the methodological framework through which organizations must evaluate and control their external providers. This sub-clause mandates the development of systematic processes rather than merely suggesting best practices.
Organizations must implement specific criteria for:
- Evaluation of potential providers before engagement
- Selection based on predetermined quality parameters
- Ongoing performance monitoring during the relationship
- Periodic re-evaluation to ensure continued conformity
The standard explicitly requires that organizations maintain documented evidence of these activities, creating an audit trail that demonstrates due diligence in supplier management. This documentation serves both as evidence of compliance and as a knowledge repository for continuous improvement.
8.4.2 Type and Extent of Control: Risk-Based Approach
Sub-clause 8.4.2 introduces the concept of proportionality in supplier control. The standard recognizes that not all external providers present equal risk to an organization's quality objectives.
The controls applied must consider:
- The potential impact of the externally provided product or service on the organization's ability to consistently meet customer requirements
- The perceived effectiveness of the controls applied by the external provider themselves
- Results from previous performance evaluations and ongoing monitoring activities
This risk-based perspective allows organizations to allocate resources efficiently, applying more rigorous controls where the quality impact is greatest. Verification activities might range from documentary evidence review to comprehensive on-site audits, depending on the criticality of the supplied item or service.
8.4.3 Information for External Providers: Ensuring Clarity
The final sub-clause addresses the critical aspect of communication with external providers. Clause 8.4.3 stipulates that organizations must clearly communicate their requirements to ensure that external providers understand precisely what is expected of them.
This communication must include:
- Detailed specifications for the products or services to be provided
- Requirements for approval methodologies
- Competency requirements for personnel involved
- The nature of interactions expected between the provider and the organization's quality management system
- Control and monitoring activities that will be applied
- Verification activities that will be conducted at the provider's premises
This comprehensive approach to communication reduces ambiguity and establishes clear parameters for the relationship, preventing quality issues that might arise from misunderstandings or incomplete information.
Before moving on, take a moment to consider how your organization currently manages supplier relationships and whether there are opportunities for improvement based on the guidelines provided by Clause 8.4.
Requirements for Supplier Management in ISO 9001:2015
ISO 9001:2015 outlines specific requirements that organizations must fulfill to ensure effective supplier management. Understanding these requirements is essential for achieving compliance and maximizing the benefits of a well-managed supply chain.
Mandatory Documentation Requirements:
- Supplier Evaluation Criteria: Organizations must document the criteria used for evaluating and selecting suppliers based on their ability to provide conforming products and services.
- Supplier Performance Records: Documentation of supplier performance evaluations, including initial assessments and periodic re-evaluations, must be maintained.
- External Provider Register: A register or list of approved suppliers must be established and maintained with their approval status.
- Verification Records: Evidence of verification activities performed on externally provided products and services must be documented.
Process Requirements:
- Risk Assessment: Organizations must conduct risk assessments for external providers based on their potential impact on the organization's ability to meet customer requirements.
- Verification Activities: Appropriate verification methods must be implemented to ensure that externally provided products and services meet specified requirements.
- Corrective Action System: A process for addressing nonconformities from suppliers must be established, including mechanisms for requesting corrective actions.
- Change Management: Systems to identify and manage changes that may affect externally provided products or services must be in place.
Communication Requirements:
- Clear Specifications: Organizations must clearly communicate all relevant specifications and requirements to external providers.
- Competence Requirements: When applicable, requirements for personnel qualifications and competencies must be communicated to suppliers.
- Interaction Requirements: The controls and interactions expected between the organization and the external provider must be clearly defined.
- Verification Activities: External providers must be informed about verification activities that will be performed at their premises.
By meeting these requirements, organizations establish a robust foundation for supplier management that supports quality objectives and ensures compliance with ISO 9001:2015 standards. These requirements integrate seamlessly with other elements of the quality management system, creating a cohesive approach to overall quality assurance.
The Importance of Supplier Evaluation in ISO 9001 Clause 8.4
Effective supplier evaluation is central to ISO 9001 Clause 8.4, as it directly impacts the quality of products and services an organization delivers. This process extends beyond basic supplier vetting to establish a comprehensive, systematic approach for ensuring suppliers consistently meet quality requirements that align with your organization's commitments to customers.
Key Criteria for ISO 9001 Supplier Evaluation:
- Quality Management Systems: Does the supplier maintain ISO 9001 certification or equivalent quality management systems that ensure consistent product/service quality?
- Performance Metrics: How does the supplier perform against established KPIs for quality, on-time delivery, and defect rates?
- Compliance Capabilities: Can the supplier demonstrate compliance with industry-specific regulations and standards relevant to your products?
- Risk Assessment: What is the supplier's risk profile regarding business continuity, geopolitical factors, and financial stability?
- Continuous Improvement: Does the supplier show commitment to ongoing process improvements and corrective action implementation?
Implementing Structured Evaluation Processes:
- Initial Qualification: Develop a standardized supplier qualification process using risk-based approaches as required by ISO 9001:2015.
- Performance Monitoring: Implement real-time monitoring systems with dashboards tracking critical supplier metrics.
- Regular Audits: Conduct scheduled on-site or remote audits based on supplier classification and risk levels.
- Documented Reviews: Maintain formal documentation of supplier evaluations to demonstrate ISO 9001 compliance during certification audits.
Managing Supplier Nonconformities:
- Establish clear escalation protocols for addressing quality issues based on severity.
- Document corrective action requests (CARs) and track their implementation through completion.
- Develop improvement plans with underperforming suppliers, setting clear expectations and timelines.
- Implement supplier development programs for strategic partners to enhance capabilities.
By integrating these ISO 9001-aligned supplier evaluation practices, organizations can significantly mitigate supply chain risks, ensure consistent product quality, and maintain compliance with certification requirements while fostering collaborative supplier relationships that drive continuous improvement.
Implementing Clause 8.4 in Your Organization: A Strategic Framework
Effective supplier management under ISO 9001:2015 Clause 8.4 requires more than compliance—it demands a strategic approach that integrates external providers into your quality ecosystem, which can be supported by our training services.
This section outlines a practical framework to establish robust supplier controls that drive organizational excellence.
Building Your Supplier Control Strategy
- Define Control Criteria with Precision
- Develop a weighted scoring matrix for supplier evaluation covering quality capabilities, financial stability, delivery reliability, and compliance history
- Align criteria with your organization's strategic objectives and risk tolerance
- Differentiate requirements based on the criticality of supplied products/services
- Implement a Rigorous Evaluation System
- Conduct structured supplier assessments through on-site audits, capability analyses, and reference checks
- Analyze performance data through statistical methods to identify trends and potential risks
- Gather cross-functional input from operations, procurement, and quality assurance teams
- Apply Strategic Selection Methods
- Categorize suppliers into tiers based on impact to your end product/service quality
- Consider total cost of ownership rather than purchase price alone
- Evaluate supplier improvement capabilities and quality management maturity
- Establish Clear Communication Channels
- Develop supplier quality agreements (SQAs) that define specific requirements and verification methods
- Create standardized technical specifications with measurable acceptance criteria
- Implement regular supplier review meetings with documented agendas and action items
- Deploy Comprehensive Monitoring Systems
- Create supplier scorecards with key performance indicators (KPIs) covering quality, delivery, responsiveness, and innovation
- Implement real-time monitoring for critical suppliers through shared data platforms
- Establish escalation protocols for performance deviations
- Drive Continuous Improvement
- Conduct quarterly performance reviews with key suppliers
- Implement supplier development programs for strategic partners
- Share best practices across your supplier network to elevate overall performance
Creating Effective Documentation
- Develop a supplier quality manual that integrates with your QMS documentation
- Maintain digital records of supplier qualifications, performance data, and corrective actions
- Implement document control procedures for supplier specifications and quality agreements
Equipping Your Team
- Provide role-specific training on supplier management techniques
- Develop competency in supplier audit methodologies and performance analysis
- Build negotiation skills for establishing quality requirements in supplier agreements
Measuring Success
- Track supplier-related nonconformities and their impact on your operations
- Measure cost savings and efficiency improvements from effective supplier management
- Monitor customer satisfaction levels related to externally provided components
By implementing this comprehensive approach, your organization will transform supplier management from a compliance exercise into a strategic advantage that enhances quality, reduces risks, and drives continuous improvement throughout your supply chain.
In the next section, we'll explore common challenges faced during supplier management and share best practices for effective supplier control.
Challenges and Best Practices for Supplier Control
Effectively managing suppliers is a complex task that involves navigating various challenges. However, by adopting best practices, organizations can overcome these obstacles and maintain high-quality standards.
Common Challenges in Supplier Management:
- Inconsistent Quality: Variances in supplier performance can lead to inconsistent product quality.
- Communication Barriers: Miscommunication with suppliers can result in misunderstandings and unmet expectations.
- Supply Chain Risks: External factors such as geopolitical events or natural disasters can disrupt supply chains.
- Compliance Issues: Ensuring suppliers adhere to industry regulations and standards can be demanding.
Best Practices for Effective Supplier Control:
- Develop Strong Relationships: Building mutual trust with suppliers can lead to better communication, collaboration, and commitment to quality.
- Implement Supplier Development Programs: Work with suppliers to improve their processes and capabilities.
- Use Technology for Better Management: Leverage supply chain management software for better visibility and control over supplier performance.
- Regular Audits and Assessments: Conduct periodic audits to ensure suppliers comply with the agreed standards and to identify areas for improvement.
Examples of Successful Supplier Control Strategies:
- Toyota's Just-In-Time (JIT) System: Toyota's famous JIT system relies heavily on supplier control to ensure parts are delivered precisely when needed, reducing inventory costs and increasing efficiency.
- Apple's Supplier Responsibility Program: Apple regularly audits its suppliers to ensure compliance with labor, environmental, and safety standards, reflecting its commitment to ethical supply chain management.
By understanding these challenges and implementing best practices, organizations can create a resilient, high-performing supplier network that supports their quality objectives.
Next, we'll examine how Clause 8.4 influences supply chain management and the broader implications for your business operations.
The Impact of Clause 8.4 on Supply Chain Management
Implementing Clause 8.4 of ISO 9001:2015 can have a transformative effect on an organization's supply chain management, leading to more resilient and responsive supply chains that are better equipped to meet customer needs and adapt to market changes.
Building a Resilient Supply Chain:
- Risk Mitigation: By evaluating and controlling suppliers, organizations can identify potential risks early and develop strategies to mitigate them.
- Diversification: Establishing a diverse base of qualified suppliers ensures that if one supplier fails, others can step in to maintain continuity of supply.
Enhancing Supplier Relationships:
- Collaboration: Working closely with suppliers to improve processes and solve problems collectively can lead to innovations and efficiency gains.
- Long-Term Partnerships: Developing long-term relationships with key suppliers can result in preferential treatment, including access to new products and services and more favorable terms.
Continuous Improvement and Clause 8.4:
- Feedback Loops: Regular reviews and audits create feedback loops for continual quality improvement in the supply chain.
- Adaptability: A focus on continual improvement helps organizations and their suppliers adapt to changing requirements and market conditions.
By embracing the principles of Clause 8.4, organizations can create supply chains that not only meet the current needs but are also future-proofed against potential disruptions.
Next, we will delve into the strategies for monitoring and reviewing supplier performance to ensure ongoing compliance with Clause 8.4 standards.
Monitoring and Reviewing Supplier Performance
Ongoing monitoring and periodic review of supplier performance are critical components of an effective supplier control process under Clause 8.4. These practices ensure that suppliers continue to meet the organization's requirements and that any issues are addressed proactively.
Techniques for Monitoring Supplier Performance:
- Key Performance Indicators (KPIs): Establish KPIs that align with quality objectives, such as on-time delivery rates, defect rates, and response times to issues.
- Scorecards and Dashboards: Use scorecards and dashboards to track supplier performance data and highlight areas requiring attention.
- Regular Audits: Schedule regular audits to verify that suppliers are adhering to agreed standards and contractual obligations.
- Supplier Surveys: Gather feedback from internal stakeholders who interact with suppliers to assess their performance from multiple perspectives.
Frequency of Reviews and Audits:
- Reviews and audits should be conducted at planned intervals, with the frequency determined by the supplier's importance and past performance.
- High-risk or critical suppliers may require more frequent evaluations, while those with a proven track record of reliability may be reviewed less often.
Making Data-Driven Decisions Based on Supplier Performance:
- Analyze performance data to identify trends and patterns that can inform strategic decisions.
- Use data to negotiate better terms, drive improvements, or make changes to the supplier base as necessary.
By systematically monitoring and reviewing supplier performance, organizations can maintain high-quality standards and foster a culture of continuous improvement within their supply chain.
Next, we will present case studies and real-world applications that illustrate the successful implementation of Clause 8.4 in various industries.
Case Studies and Real-world Applications
Learning from real-world examples provides valuable insights into the practical application of Clause 8.4 - Supplier Control in ISO 9001:2015. These case studies demonstrate the tangible benefits organizations can achieve by effectively managing their suppliers.
Example of a Company Excelling in Supplier Control:
- XYZ Manufacturing: XYZ Manufacturing implemented a comprehensive supplier control system that included stringent evaluation criteria, regular performance audits, and a collaborative approach to problem-solving with suppliers. As a result, they saw a 30% reduction in product defects and a 20% improvement in on-time delivery from their suppliers.
Lessons Learned from Supplier Control Implementation:
- Effective Communication: Clear and consistent communication with suppliers is crucial for conveying expectations and addressing issues promptly.
- Supplier Involvement: Involving suppliers in the process of setting quality objectives and expectations leads to better buy-in and performance.
- Flexibility and Adaptability: Being flexible and adaptable in the management approach allows for adjustments based on supplier feedback and performance data.
How Clause 8.4 Has Transformed Supplier Management for Businesses:
- Service Industry Case: A service company used Clause 8.4 guidelines to enhance their IT vendor management, leading to improved service quality and customer satisfaction.
- Retail Example: A retail chain applied supplier control principles to its sourcing strategy, resulting in more sustainable products and a stronger brand reputation.
These case studies underscore the effectiveness of ISO 9001:2015's Clause 8.4 in driving quality improvements and operational efficiencies through strategic supplier management.
As we conclude this section, consider how your organization can draw inspiration from these examples to strengthen your supplier control processes.
Frequently Asked Questions on Clause 8.4 - Supplier Control
When it comes to implementing Clause 8.4 - Supplier Control in ISO 9001:2015, there are several common questions that arise. Addressing these FAQs can help clarify the process and underscore the importance of this clause in the quality management system.
How often should supplier evaluations be conducted?
Supplier evaluations should be conducted based on the significance of the supplier to your business and their past performance. High-risk suppliers, or those providing critical components, may require more frequent evaluations, while those with a consistent track record of reliability might be reviewed less often. It's also important to reassess suppliers whenever there are changes in their services or in your requirements.
Can small businesses benefit from implementing Clause 8.4?
Absolutely. While the scope and complexity of supplier control processes may vary, small businesses can still see significant benefits from implementing Clause 8.4. It can lead to better product quality, fewer disruptions, and improved customer satisfaction, regardless of company size.
How does technology aid in supplier control?
Technology plays a pivotal role in supplier control by providing tools for better data management, communication, and performance tracking. Supply chain management software can automate many aspects of supplier control, from tracking KPIs and generating performance reports to facilitating communication and document control.
By addressing these questions, organizations can better understand how to apply Clause 8.4 effectively within their quality management system.
Next, we'll wrap up our discussion with a conclusion that summarizes the key points of this comprehensive guide on Clause 8.4 - Supplier Control in ISO 9001:2015.
Conclusion
In this comprehensive guide, we've explored the intricacies of Clause 8.4 - Supplier Control within ISO 9001:2015, demonstrating its vital role in ensuring the quality of products and services. By implementing this clause effectively, organizations can extend their quality management systems beyond their immediate operations to include the entire supply chain, resulting in enhanced overall quality and customer satisfaction.
Key Takeaways:
- Supplier control is crucial for maintaining product and service quality.
- A systematic approach to supplier evaluation and selection is essential.
- Regular monitoring and continuous improvement are vital for supplier management.
- Building strong relationships with suppliers can lead to better outcomes.
- Challenges in supplier management can be mitigated through best practices.
Remember, the goal of Clause 8.4 is not only to control but also to collaborate with suppliers in a way that fosters mutual growth and success. By following the guidelines and principles outlined in ISO 9001:2015, organizations can achieve a harmonious balance between managing supplier risks and nurturing beneficial partnerships.
We encourage all businesses to prioritize the implementation of Clause 8.4 and to continuously seek ways to improve their supplier control processes. The rewards of doing so—improved reliability, stronger supply chains, and heightened customer trust—are well worth the effort.
Next Steps:
Ready to enhance your supplier control processes? Start by exploring our ISO 9001 certification consulting services to align your organization with Clause 8.4 standards. Need tailored guidance? Book a call with our experts to discuss your specific needs, or dive deeper into our quality training resources to equip your team for success.