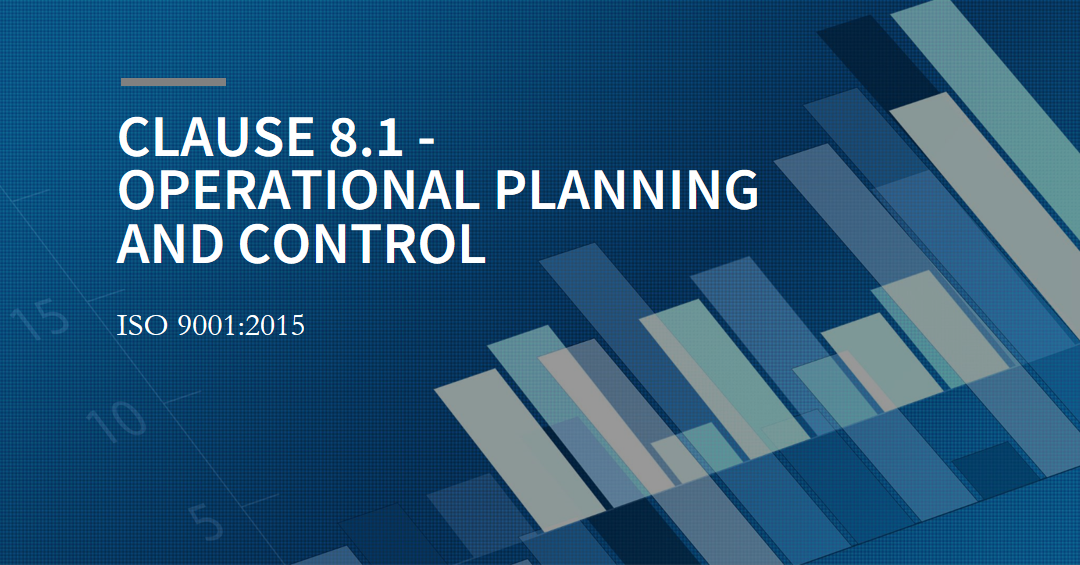
Introduction
In the world of business management and quality control, Clause 8.1 - Operational Planning and Control stands out as a cornerstone for ensuring that organizational processes align with strategic objectives. This clause, often found within internationally recognized standards like ISO, outlines the necessary steps and considerations businesses must take to effectively plan, implement, and manage their operational processes.
The significance of Clause 8.1 cannot be overstated. It's not just a set of guidelines but a strategic enabler that can lead to significant improvements in efficiency, customer satisfaction, and overall business performance. By understanding and applying the principles of Operational Planning and Control, organizations can navigate complex market conditions, adapt to changing customer demands, and maintain a competitive edge.
Why Should Businesses Care About Clause 8.1?
- Alignment with Business Goals: Proper operational planning ensures that every process contributes to the broader company objectives.
- Resource Optimization: Clause 8.1 helps businesses use their resources more efficiently, reducing waste and increasing profitability.
- Risk Management: Planning and control mechanisms are vital for identifying and mitigating potential risks before they become issues.
- Continuous Improvement: It sets the stage for ongoing evaluation and enhancement of operational processes.
In this comprehensive guide, we will delve deep into the intricacies of Clause 8.1, exploring its components, implementation strategies, and real-world applications. Whether you're a seasoned professional or new to the concept, you'll find actionable insights that can transform your operational planning and control processes.
Let's begin by dissecting what Clause 8.1 entails and how it forms the backbone of effective operational management.
Understanding Clause 8.1 - Operational Planning and Control
Clause 8.1 - Operational Planning and Control is the guiding force behind how an organization establishes, implements, controls, and maintains its operational processes. It is an integral part of management systems standards, such as ISO 9001 (Quality Management Systems), and serves as a blueprint for aligning operations with the strategic direction of the company.
What is Operational Planning and Control?
Operational Planning and Control refers to the systematic approach to managing the core business processes that produce and deliver the organization's products or services. It encompasses everything from resource allocation to workflow management, with a focus on efficiency and effectiveness.
The Framework and Principles
The framework of Clause 8.1 is built on the Plan-Do-Check-Act (PDCA) cycle, which encourages organizations to:
- Plan: Identify objectives and processes necessary to deliver results in accordance with customer requirements and the organization's policies.
- Do: Implement the processes as planned.
- Check: Monitor and measure processes against policies, objectives, and requirements for the product or service, and report results.
- Act: Take actions to continually improve process performance.
Adherence to these principles ensures a methodical approach to operational planning and fosters a culture of continuous improvement.
Objectives of Clause 8.1
The primary objectives of implementing Clause 8.1 include:
- Providing a consistent approach to operational processes to ensure quality and reliability.
- Ensuring that the organization can meet its stated commitments in an efficient manner.
- Enabling the organization to respond quickly to new opportunities and challenges.
By fully understanding Clause 8.1, businesses can lay the groundwork for operational excellence. With this foundation in place, we can explore the specific components that make up this crucial clause.
The Components of Clause 8.1
Clause 8.1 - Operational Planning and Control is composed of several key elements that together create a robust framework for managing business operations. Understanding each component is essential for effectively applying the clause to your organization's processes.
Detailed Breakdown of Key Elements
- Establishing Criteria for Operational Processes:
- Define clear criteria for the design, development, and delivery of products and services.
- Ensure criteria are documented and understood by relevant personnel.
- Control of Operational Planning and Control:
- Implement control measures to manage the operational processes according to the established criteria.
- Monitor the effectiveness of these controls and make necessary adjustments.
- Management of Resources:
- Assess and provide the resources needed for optimal operation, including human resources, infrastructure, and environment for the operation of processes.
- Change Management:
- Develop a systematic approach to manage changes in operational processes to prevent unintended consequences.
- Document and review changes to maintain control and continuity.
- Operational Risk Management:
- Identify potential risks and opportunities associated with operational processes.
- Implement actions to address these risks and leverage opportunities for improvement.
How Each Component Contributes to Overall Operational Efficiency
Each component of Clause 8.1 plays a vital role in enhancing operational efficiency:
- Establishing Criteria ensures consistency and clarity, which drives process efficiency and quality outputs.
- Control Measures provide a mechanism for maintaining process integrity, which leads to reliable and predictable results.
- Resource Management ensures that the right resources are available at the right time, which minimizes downtime and maximizes productivity.
- Change Management ensures that any alterations to the process are well-managed, thereby preventing disruptions and maintaining efficiency.
- Risk Management minimizes potential setbacks and maximizes the potential for process optimization and innovation.
Relationship Between Clause 8.1 and Continuous Improvement Processes
Clause 8.1 is designed to not only establish a strong operational foundation but also to encourage ongoing evaluation and refinement of processes. This aligns with the principles of continuous improvement, which is central to many quality management systems. By regularly reviewing and improving operational processes, organizations can adapt to changing market conditions, customer needs, and technological advancements, ensuring long-term success.
The Implementation Process of Clause 8.1
Implementing Clause 8.1 - Operational Planning and Control into an organization's processes requires a structured approach. This section outlines the steps involved in integrating this important clause into your business operations.
Step-by-Step Guide on Implementing Operational Planning and Control
- Assessment of Current Processes:
- Begin with a thorough evaluation of existing procedures to identify gaps and areas for improvement.
- Engage with various stakeholders, including employees, customers, and suppliers, to gain a comprehensive understanding of current operational performance.
- Development of Operational Criteria:
- Based on the assessment, establish clear operational criteria that align with business objectives and customer requirements.
- Ensure these criteria are realistic, measurable, and tailored to your organization's capabilities.
- Resource Allocation:
- Determine the resources required to meet the established criteria, including personnel, technology, and financial investment.
- Plan for resource allocation that supports the efficient execution of operational processes.
- Process Design and Documentation:
- Design processes that meet the established operational criteria, utilizing best practices and industry standards where applicable.
- Document these processes in a clear and accessible manner, ensuring that all relevant team members are informed and trained.
- Implementation of Control Measures:
- Apply control measures to manage and monitor operational processes, ensuring they remain within defined parameters.
- Use data and feedback to adjust controls as needed for continual process optimization.
- Change Management Procedures:
- Create a formal change management process to handle any modifications to operations, ensuring that changes are planned, communicated, and documented effectively.
- Risk Assessment and Mitigation:
- Regularly perform risk assessments to identify potential issues that could impact operational efficiency or quality.
- Develop and implement mitigation strategies to address identified risks proactively.
Best Practices for Integrating Clause 8.1
- Engage Leadership: Ensure top management is involved and supportive of the implementation efforts.
- Employee Training: Provide comprehensive training to employees on Clause 8.1 principles and their role in operational planning and control.
- Communication: Maintain open lines of communication throughout the organization to facilitate feedback and collaborative problem-solving.
- Technology Utilization: Leverage technology to streamline processes, improve data collection, and enhance monitoring capabilities.
Common Challenges and Solutions
- Resistance to Change: Overcome resistance by involving employees in the planning process and clearly communicating the benefits of Clause 8.1 implementation.
- Resource Constraints: Prioritize resource allocation based on critical processes and consider outsourcing or partnerships to fill gaps.
- Maintaining Documentation: Use document management systems to keep process documentation organized, up-to-date, and readily accessible.
Implementing Clause 8.1 - Operational Planning and Control is an ongoing commitment to excellence. By following these steps and best practices, businesses can build a strong foundation for operational efficiency and continuous improvement.
Clause 8.1 in Action: Case Studies
To illustrate the practical benefits of implementing Clause 8.1 - Operational Planning and Control, we'll examine case studies from different industries where the clause has been successfully applied.
Real World Example: Manufacturing Industry
Challenge: A manufacturing company was facing production inefficiencies, leading to delays and increased waste.
Implementation of Clause 8.1:
- Operational Criteria Establishment: The company set clear production targets and quality standards.
- Control Measures: Introduced real-time monitoring systems for equipment and processes.
- Change Management: Implemented a structured approach to manage equipment upgrades and process changes.
- Risk Management: Conducted regular risk assessments to identify potential disruptions in the supply chain.
Outcome: The company saw a 20% increase in production efficiency and a significant reduction in material waste, leading to cost savings and improved customer satisfaction.
Real World Example: IT Services
Challenge: An IT service provider struggled with project delivery times and inconsistent service quality.
Implementation of Clause 8.1:
- Resource Allocation: Allocated skilled resources to key projects and invested in employee training.
- Process Documentation: Standardized project management methodologies and documented all processes.
- Control Measures: Set up quality assurance checks and milestones throughout project lifecycles.
- Risk Assessment: Identified potential IT security risks and developed a response plan.
Outcome: The provider improved project delivery times by 15% and achieved higher service consistency, enhancing their market reputation.
Real World Example: Healthcare Sector
Challenge: A hospital was experiencing long patient wait times and operational bottlenecks.
Implementation of Clause 8.1:
- Operational Criteria: Defined patient service standards and established triage protocols.
- Resource Management: Optimized staff schedules and introduced new patient management software.
- Change Management: Trained staff on new protocols and involved them in process improvements.
- Risk Management: Implemented a system for real-time tracking of patient flow and resource utilization.
Outcome: Patient wait times were reduced by 30%, and overall patient throughput increased, resulting in higher patient satisfaction scores.
These case studies demonstrate the tangible benefits of Clause 8.1 in optimizing operations, enhancing quality, and improving customer experiences across various sectors.
Operational Planning and Control Tools and Techniques
Implementing Clause 8.1 - Operational Planning and Control effectively requires the use of various tools and techniques. These resources assist in planning, monitoring, and improving operational processes.
Overview of Tools and Software That Facilitate Clause 8.1 Implementation
- Project Management Software:
- Tools like Asana, Trello, and Microsoft Project help in organizing tasks, deadlines, and collaborations.
- Process Mapping Software:
- Applications such as Lucidchart and Visio provide visual representations of processes, making it easier to identify inefficiencies and areas for improvement.
- Quality Management Systems (QMS):
- Comprehensive software solutions like Ryze’s ISO 9001 Software are designed to manage documentation, compliance, audits, and continuous improvement, all aligned with Clause 8.1 requirements.
- Risk Management Tools:
- Software like RiskWatch and LogicManager offer structured approaches to identifying, assessing, and mitigating operational risks.
- Resource Management Tools:
- Platforms such as Float and Smartsheet enable organizations to allocate and track resources efficiently.
Techniques to Enhance Operational Planning and Control Procedures
- Six Sigma and Lean Methodologies: Utilize these methodologies to reduce waste and improve process efficiency.
- PDCA Cycle: Apply the Plan-Do-Check-Act cycle for continuous process evaluation and refinement.
- Root Cause Analysis (RCA): Use RCA to identify the underlying causes of operational issues and address them effectively.
Tips for Selecting the Right Tools for Your Business Needs
- Assess Compatibility: Ensure the tools align with your business processes and technological infrastructure.
- Evaluate Features: Look for features that specifically support the components of Clause 8.1, such as process mapping, risk assessment, and change management.
- Consider Scalability: Choose tools that can grow with your business and adapt to changing operational
Monitoring and Measuring the Effectiveness of Clause 8.1
To ensure that the implementation of Clause 8.1 - Operational Planning and Control is delivering the desired results, it's crucial to monitor and measure its effectiveness regularly.
Establishing KPIs for Operational Planning and Control
Key Performance Indicators (KPIs) are vital for tracking the performance of operational processes. Here are some examples of KPIs relevant to Clause 8.1:
- Cycle Time: The time taken to complete a process from start to finish.
- Defect Rate: The percentage of errors or defects in the final product or service.
- Resource Utilization: How effectively resources are being used in the operational process.
- Customer Satisfaction: Feedback and ratings provided by customers regarding their experience with the product or service.
Techniques for Monitoring Compliance and Performance
- Regular Audits: Conduct internal and external audits to ensure compliance with operational criteria and identify areas for improvement.
- Performance Dashboards: Implement dashboards that provide real-time data on KPIs, allowing for quick responses to operational challenges.
- Employee Feedback: Engage with employees to gain insights into the day-to-day functioning of processes and potential issues.
How to Use Feedback and Data to Refine Operational Planning Processes
- Data Analysis: Examine the collected data to identify trends, patterns, and anomalies.
- Feedback Loops: Create mechanisms for feedback to be channeled back into the operational planning process, ensuring that it informs future improvements.
- Action Plans: Develop and implement action plans based on the analysis and feedback to address any deficiencies or capitalize on opportunities for enhancement.
Through effective monitoring and measuring, organizations can ensure that Clause 8.1's implementation is not only compliant but also contributes to the ongoing success and competitiveness of the business.
Integrating Clause 8.1 with Other Management Systems
Clause 8.1 - Operational Planning and Control is not an isolated element; it is most effective when integrated with other management systems within an organization. This holistic approach can optimize business performance and create a seamless operational environment.
Synergies Between Clause 8.1 and Other Management System Clauses
The principles of Clause 8.1 complement various aspects of other management system standards, such as:
- ISO 9001 (Quality Management): Aligns with quality objectives and the enhancement of customer satisfaction.
- ISO 14001 (Environmental Management): Supports sustainable operational processes and environmental responsibility.
- ISO 45001 (Occupational Health and Safety): Intersects with the commitment to providing a safe working environment.
Strategies for a Holistic Approach to Operational Planning and Control
- Cross-Functional Teams: Establish teams that include members from different departments to foster a unified approach to operational planning.
- Integrated Audits: Conduct audits that cover multiple management system standards to ensure cohesive compliance and identify improvement opportunities.
- Unified Documentation: Create documentation that reflects the integration of various management systems, streamlining processes and communication.
The Benefits of Integrating Clause 8.1 with Quality Management Systems
- Consistency in Processes: A unified approach ensures that operational planning is consistent with quality management principles, leading to more predictable outcomes.
- Efficiency Gains: Integration can eliminate duplicate efforts and streamline processes, saving time and resources.
- Enhanced Risk Management: A comprehensive management system approach allows for more robust risk assessments and mitigation strategies.
Integrating Clause 8.1 with other management systems can lead to a stronger, more resilient, and more competitive organization, fully equipped to meet the diverse demands of the modern business environment.
Training and Competence in Operational Planning and Control
For Clause 8.1 - Operational Planning and Control to be effectively implemented, it is critical that the staff involved in operational processes are well-trained and competent. This ensures that they can carry out their duties effectively, leading to better overall performance and compliance.
Identifying Necessary Skills for Effective Implementation of Clause 8.1
To begin with, organizations must identify the specific skills and knowledge required for their operational planning and control processes. This may include:
- Technical Expertise: Understanding the technical aspects of the products or services being offered.
- Process Management: Skills in managing and improving operational processes.
- Risk Assessment: Ability to identify and mitigate potential risks.
- Quality Control: Knowledge of quality standards and measurement techniques.
Designing a Training Program for Staff on Operational Planning and Control
A comprehensive training program should cover:
- Clause 8.1 Overview: Educating staff on the importance and objectives of Clause 8.1.
- Specific Process Training: Detailed training on the operational processes they will be involved in.
- Tools and Software: Instructions on how to use any tools or software that support Clause 8.1 implementation.
- Continuous Improvement: Training on how to identify opportunities for process improvement.
Measuring the Impact of Training on Operational Performance
To measure the effectiveness of the training program, consider the following metrics:
- Performance Improvements: Monitor changes in operational KPIs following training.
- Error Rates: Track error rates before and after training to gauge understanding and competence.
- Employee Feedback: Gather feedback from employees on the training's relevance and helpfulness.
- Assessment Scores: Use assessments to measure the knowledge and skills gained from the training.
Investing in the training and development of employees not only supports the successful implementation of Clause 8.1 but also fosters a culture of excellence and continuous learning within the organization.
Continuous Improvement and Clause 8.1
Clause 8.1 - Operational Planning and Control is not a static concept; it is intrinsically linked to the idea of continuous improvement within an organization. The successful application of Clause 8.1 inherently demands a commitment to ongoing enhancement of operational processes.
The Role of Clause 8.1 in Driving Continuous Improvement in Operations
The iterative nature of Clause 8.1, with its emphasis on the Plan-Do-Check-Act (PDCA) cycle, positions it as a natural driver for continuous improvement. By consistently applying Clause 8.1, organizations can achieve:
- Incremental Process Enhancements: Regularly updating and refining operational processes based on performance data and feedback.
- Adaptability and Responsiveness: The ability to quickly adapt operational strategies in response to internal and external changes.
- Innovation: Encouraging innovation by constantly seeking ways to improve efficiency and effectiveness.
Techniques for Fostering a Culture of Continuous Improvement Through Clause 8.1
- Employee Empowerment: Encourage staff at all levels to contribute ideas for process improvement.
- Recognition and Rewards: Implement a system to recognize and reward contributions to process enhancements.
- Regular Reviews: Schedule periodic reviews of operational processes to identify improvement opportunities.
- Benchmarking: Compare operational performance against industry standards or competitors to identify areas for improvement.
Real World Example on Continuous Improvement Driven by Operational Planning and Control
Case Study 1: Automotive Manufacturer
A leading automotive manufacturer implemented Clause 8.1 to streamline their production line. Through continuous review and improvement of their operational processes, they were able to reduce assembly times by 25% and improve overall product quality.
Case Study 2: Software Development Firm
An agile software development firm applied the principles of Clause 8.1 to their project management processes. By continuously adapting their methodologies based on client feedback and project outcomes, they achieved a 40% increase in customer satisfaction.
The journey of continuous improvement is never-ending, and Clause 8.1 provides the structure and guidance necessary to navigate this path effectively. By embracing the principles of Clause 8.1, organizations can foster a culture that perpetually seeks to improve, adapt, and excel.
Clause 8.1 - Operational Planning and Control in Different Industries
The principles embodied in Clause 8.1 - Operational Planning and Control are universally applicable across a wide range of industries. Each sector can tailor these principles to fit its unique operational demands and regulatory requirements. Let's examine the application of Clause 8.1 in various industries and the specific benefits it provides.
Application of Clause 8.1 Across Various Sectors
- Manufacturing: Streamlines production processes, reduces waste, and increases efficiency.
- Healthcare: Enhances patient care coordination, improves treatment outcomes, and ensures compliance with health regulations.
- Information Technology: Facilitates project management, accelerates software development cycles, and improves service delivery.
- Finance and Banking: Strengthens risk management, ensures compliance with financial regulations, and improves customer service.
- Retail: Optimizes supply chain management, enhances inventory control, and improves customer experience.
Customizing Operational Planning and Control Practices to Industry-Specific Needs
Each industry faces distinct challenges and requirements that need to be considered when implementing Clause 8.1:
- Regulatory Compliance: Tailoring processes to meet industry-specific regulatory requirements.
- Technology Integration: Utilizing industry-specific technologies to optimize operational planning and control.
- Quality Standards: Adhering to industry-specific quality standards and customer expectations.
Future Trends in Operational Planning and Control
As the business landscape continues to evolve, fueled by technological advancement and changing market conditions, operational planning and control must adapt to remain effective. Clause 8.1 - Operational Planning and Control is poised to play a pivotal role in shaping these future trends.
Emerging Trends and Innovations in Operational Planning
- Data Analytics and AI: Increased use of data analytics and artificial intelligence to predict trends, optimize operations, and personalize customer experiences.
- Internet of Things (IoT): IoT devices providing real-time monitoring of equipment and processes for proactive maintenance and efficiency improvements.
- Automation and Robotics: Greater adoption of automation and robotics to perform repetitive tasks, reducing human error and freeing up staff for higher-value activities.
The Evolving Role of Technology in Clause 8.1 Applications
Technology will increasingly be integrated into the fabric of operational planning and control, as outlined in Clause 8.1:
- Cloud Computing: Cloud-based systems will enhance collaboration and accessibility of operational data across geographic locations.
- Blockchain: Blockchain technology may be used for secure and transparent supply chain management.
- Virtual and Augmented Reality (VR/AR): VR and AR can be utilized for training purposes and to simulate operational changes before implementation.
Predictions on How Clause 8.1 Will Shape Future Business Operations
- Sustainability: Clause 8.1 will likely emphasize sustainable practices as businesses become more environmentally conscious.
- Customization: Operational planning and control will become more tailored to individual customer needs and preferences.
- Resilience: A greater focus on building resilient operations that can withstand disruptions such as those experienced during the COVID-19 pandemic.
The future of operational planning and control is dynamic and exciting, with Clause 8.1 continually adapting to guide organizations through the changing tides of business practices.
Conclusion
Clause 8.1 - Operational Planning and Control serves as a critical component of effective business management, offering a structured approach to aligning operational processes with organizational goals. Throughout this comprehensive guide, we've explored the depth and breadth of Clause 8.1, from its core principles and implementation steps to its real-world applications across various industries.
Key Takeaways:
- Strategic Alignment: Clause 8.1 ensures that operational activities are in harmony with the strategic objectives of the organization.
- Efficiency and Consistency: By establishing and monitoring clear operational criteria, businesses can achieve greater efficiency and produce consistent results.
- Risk Management: Proactive identification and mitigation of risks are central to maintaining operational stability.
- Continuous Improvement: The iterative nature of Clause 8.1 fosters a culture of ongoing enhancement, driving innovation and competitiveness.
The value of Clause 8.1 transcends industry boundaries, offering a universal framework that can be adapted to the unique challenges and requirements of each business sector. As we look to the future, Clause 8.1 will continue to evolve, integrating emerging trends and technologies to guide organizations towards operational excellence.
Embracing Clause 8.1 is not just about compliance; it's about seizing the opportunity to excel in an increasingly complex and competitive business environment. It's about committing to a journey of continuous improvement, where operational planning and control become the engines of sustainable growth and success.
Frequently Asked Questions (FAQs)
Q: What is Clause 8.1 - Operational Planning and Control?A: Clause 8.1 refers to the segment within management system standards that outlines the requirements for planning, implementing, controlling, and maintaining operational processes in alignment with business objectives.
Q: Why is Clause 8.1 important for businesses?A: It provides a structured framework for ensuring operational processes are efficient, consistent, and adaptable, leading to improved quality, risk management, and customer satisfaction.
Q: Can Clause 8.1 be integrated with other management systems?A: Yes, Clause 8.1 is designed to work in conjunction with other management system standards, such as ISO 9001, ISO 14001, and ISO 45001, creating a cohesive approach to business operations.
Q: How do businesses monitor the effectiveness of Clause 8.1?A: Organizations use Key Performance Indicators (KPIs), regular audits, performance dashboards, and employee feedback to monitor and measure the effectiveness of their operational planning and control processes.
Call to Action
Are you ready to harness the full potential of Clause 8.1 - Operational Planning and Control within your organization? Take the first step by assessing your current operational processes against the principles outlined in this guide. Identify areas for improvement, and begin the journey toward enhanced operational efficiency and sustainability.
For further guidance, support, or to discuss how to customize Clause 8.1 for your specific industry needs, feel free to reach out. Let's work together to transform your operational planning and control processes into a source of strategic advantage.
If you have any questions or need assistance, our team is here to support your commitment to operational excellence. Contact us today to elevate your business operations to new heights.