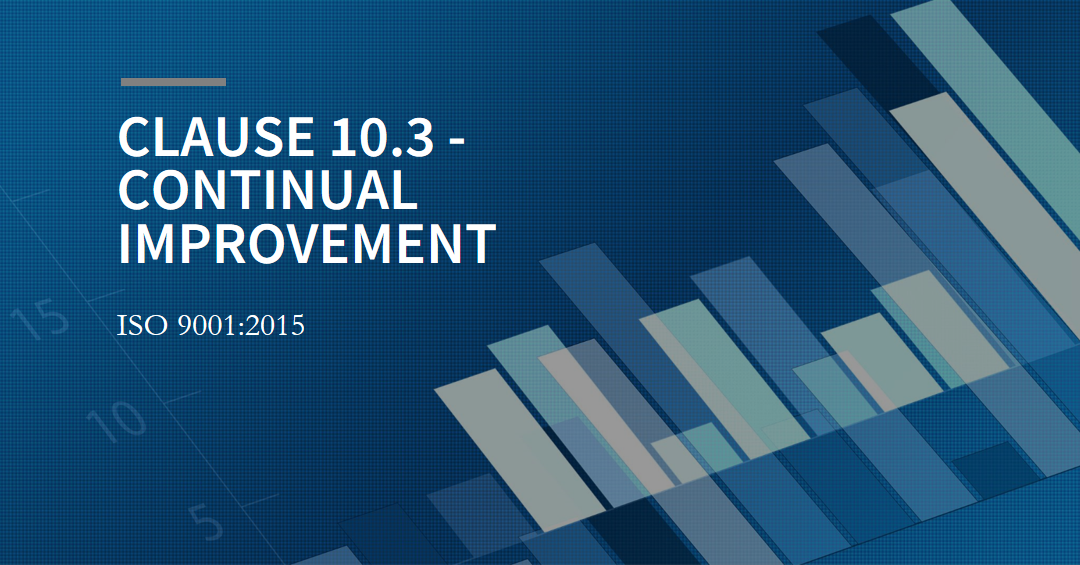
Introduction to ISO 9001:2015
In an ever-evolving business landscape, the quest for quality is unending. ISO 9001:2015 stands as a beacon of excellence, a standardized approach to quality management systems (QMS) that organizations around the globe strive to attain and maintain. This internationally recognized standard is not just a badge of honor; it is a blueprint for streamlining processes, enhancing customer satisfaction, and ultimately, driving business growth.
At the heart of ISO 9001:2015 lies the commitment to continual improvement—a principle that ensures businesses are never stagnant but are always pushing the envelope to be better. Clause 10.3 - Continual Improvement is a critical component of this standard, emphasizing the need for ongoing refinement of the QMS.
Why is continual improvement so significant? In a word, sustainability. Companies that embed continual improvement into their culture can adapt to changes in the market, meet customer expectations more effectively, and stay ahead of the competition. Continual improvement is not a one-off project; it is an ongoing journey towards excellence.
In this blog post, we will delve deep into Clause 10.3 - Continual Improvement of ISO 9001:2015, exploring its nuances and how it can be the catalyst for a thriving, quality-centered business. Let's embark on this journey of discovery, where quality is not a destination but a path we tread upon diligently.
Understanding Clause 10.3 - Continual Improvement
The essence of Clause 10.3 within the ISO 9001:2015 framework is the establishment of an ongoing process of enhancement across all aspects of an organization's quality management system. This clause is not merely about fixing what is broken; it is about proactively seeking ways to make good processes great and maintaining an organizational culture that thrives on making incremental improvements over time.
Objectives of Continual Improvement
The objectives of continual improvement within ISO 9001:2015 are manifold:
- Enhancing Customer Satisfaction: By constantly improving products and services.
- Optimizing Operational Efficiency: Through the refinement of processes and elimination of waste.
- Increasing Flexibility: Allowing organizations to adapt swiftly to changes in their environment or market.
- Fostering Innovation: Encouraging a culture where new ideas are welcomed and tested.
- Building a Sustainable Business: Ensuring the long-term health and success of the organization.
The Role of Continual Improvement in Quality Management
Continual improvement acts as the engine of a quality management system. It drives the system forward and ensures that it evolves with the changing needs of customers and the business environment. By integrating continual improvement into every facet of the organization, businesses ensure that their quality management system remains dynamic and robust.
Clause 10.3 calls for organizations to:
- Review the performance of the QMS regularly.
- Identify opportunities for improvement and innovation.
- Implement necessary actions to enhance the overall performance.
- Evaluate the effectiveness of these actions.
Implementing continual improvement is a strategic decision that can lead to substantial benefits, including improved quality, reduced costs, and increased market share.
The Principles of Continual Improvement
Continual improvement in ISO 9001:2015 is underpinned by several key principles that align with the overall quality management philosophy. Understanding these principles is essential for organizations seeking to fully embrace the spirit of Clause 10.3.
Customer Focus
The primary goal of any quality management system is to meet and exceed customer expectations. Continual improvement initiatives should always consider the impact on the customer, aiming to enhance the customer experience and build long-term relationships.
Leadership and Commitment
Leadership plays a crucial role in driving continual improvement. Management must demonstrate commitment by providing the necessary resources, setting clear goals, and leading by example. This commitment helps to foster a culture where improvement is always on the agenda.
Engagement of People
Employees at all levels are the essence of an organization and their full involvement enables their abilities to be used for the organization’s benefit. Engaging staff in the process of continual improvement ensures that ideas and insights from those closest to the work are captured and acted upon.
Process Approach
Understanding and managing interrelated processes as a system contributes to the organization's effectiveness and efficiency in achieving its objectives. Continual improvement focuses on optimizing these processes to deliver consistent and predictable results.
Improvement
Improvement is a perpetual objective for the organization. It is necessary to maintain current levels of performance, to react to changes in the internal and external conditions, and to create new opportunities.
Evidence-Based Decision Making
Decisions based on the analysis and evaluation of data and information are more likely to produce desired results. Continual improvement relies on measuring and analyzing the performance of processes and making informed decisions based on this data.
Relationship Management
For sustained success, an organization manages its relationships with interested parties, such as suppliers. Strong relationships can lead to shared improvement objectives and synergies that benefit all parties involved.
By adhering to these principles, organizations can ensure that their efforts towards continual improvement are effective and lead to significant benefits for all stakeholders involved.
Implementing Continual Improvement
To actualize the principle of continual improvement outlined in Clause 10.3 of ISO 9001:2015, organizations need to establish a systematic approach. This approach should be integral to the organization's operations and should be revisited regularly to ensure its effectiveness.
Planning for Improvement
The first step in implementing continual improvement is to develop a clear plan that outlines:
- Objectives: What the organization aims to achieve through improvement.
- Benchmarks: Current performance metrics that improvements can be measured against.
- Resources: The human, technological, and financial resources needed.
- Timeline: Reasonable timeframes for achieving improvement milestones.
Identifying Areas for Improvement
Organizations should adopt a methodical approach to identify areas in need of enhancement:
- Customer Feedback: Direct insights from customers can highlight areas for improvement.
- Employee Suggestions: Staff who are involved in the daily operations often have valuable ideas for making processes more efficient.
- Audit Results: Regular internal and external audits can uncover systemic issues that require attention.
Involving Employees in the Improvement Process
Creating a culture of improvement involves:
- Training: Equipping employees with the skills to identify and implement improvements.
- Empowerment: Giving staff the authority to make changes and contribute ideas.
- Recognition: Acknowledging and rewarding contributions to the improvement process.
Techniques for Fostering a Culture of Improvement
- Regular Communication: Keeping all stakeholders informed about improvement initiatives and progress.
- Inclusive Decision-Making: Inviting input from various levels of the organization when planning improvements.
- Continuous Learning: Encouraging employees to learn from successes and failures to drive future improvements.
By following these steps, organizations can embed continual improvement into their daily operations, ensuring that improvement is not just a goal but a natural part of the organizational culture.
Tools and Techniques for Continual Improvement
For Clause 10.3 - Continual Improvement to be effectively implemented in ISO 9001:2015, organizations can leverage various tools and techniques that aid in identifying, planning, and executing improvement strategies.
The Plan-Do-Check-Act (PDCA) Cycle
The PDCA cycle is a four-step model for carrying out change:
- Plan: Identify an opportunity and plan for change.
- Do: Implement the change on a small scale.
- Check: Use data to analyze the results of the change and determine whether it made a difference.
- Act: If the change was successful, implement it on a wider scale and continuously assess your results. If the change did not work, begin the cycle again.
Root Cause Analysis
When problems arise, it's essential to understand their root cause before attempting to solve them. Techniques such as the "5 Whys" and fishbone diagrams help to drill down to the underlying cause of an issue, ensuring that solutions are effective and prevent recurrence.
Six Sigma and Lean Methodologies
- Six Sigma: Focuses on reducing variation and improving process quality by identifying and removing the causes of defects.
- Lean: Aims to streamline production by reducing waste and increasing efficiency.
Use of Quality Management Tools
Various tools can be used to support continual improvement efforts:
- Pareto Charts: Help to identify the most significant problems to tackle.
- Fishbone Diagrams: Used to brainstorm potential causes of a problem.
- Control Charts: Monitor processes over time and identify trends or shifts in a process.
By utilizing these tools and techniques, organizations can systematically approach continual improvement, ensuring that efforts are well-planned, executed, and measured for effectiveness.
Measuring and Monitoring Improvement
A critical aspect of Clause 10.3 - Continual Improvement in ISO 9001:2015 is the ability to measure and monitor the effectiveness of the improvements made. This ensures that the organization can validate the impact of changes and sustain the momentum of its quality management efforts.
Setting Measurable Objectives
Objectives for improvement must be Specific, Measurable, Achievable, Relevant, and Time-bound (SMART). These objectives provide a clear target for the organization and a way to gauge progress.
- Specific: Objectives should be clear and focused.
- Measurable: There should be a way to measure success.
- Achievable: Objectives should be realistic and attainable.
- Relevant: Goals should align with broader business objectives.
- Time-bound: There should be a deadline for achieving the objective.
Tracking Progress Against Objectives
Continuous monitoring is vital for understanding whether the changes made are producing the desired outcomes. Organizations can track progress through:
- Performance Indicators: These metrics provide insight into how well a process is functioning.
- Milestone Reviews: Regularly scheduled reviews can help ensure that improvement projects are on track and allow for adjustments if necessary.
- Benchmarking: Comparing performance against industry standards or competitors can help set realistic improvement targets.
Internal Audits and Feedback Mechanisms
Internal audits are a key tool for assessing the QMS and identifying areas for improvement. Feedback mechanisms, such as surveys and suggestion boxes, can provide valuable insights from employees and customers.
Using KPIs to Monitor Continual Improvement
Key Performance Indicators (KPIs) should be established for each area of improvement. These indicators should:
- Be Aligned: Relate directly to the SMART objectives set for the improvement.
- Be Balanced: Cover different aspects of performance, such as quality, timeliness, and customer satisfaction.
- Provide Insights: Help the organization understand the cause-and-effect relationship between actions taken and outcomes achieved.
By effectively measuring and monitoring improvement, an organization can not only assess the impact of its efforts but also demonstrate its commitment to maintaining a high-quality management system to stakeholders.
Challenges in Continual Improvement
While the pursuit of continual improvement is a noble and necessary endeavor for any organization committed to quality, it is not without its challenges. Recognizing and addressing these challenges is essential for the successful implementation of Clause 10.3 in ISO 9001:2015.
Overcoming Resistance to Change
Change can be uncomfortable, and it is natural for employees to resist new ways of working. Overcoming this resistance involves:
- Communication: Clearly explaining the reasons for change and the benefits it will bring.
- Involvement: Engaging employees in the change process to give them a sense of ownership.
- Support: Providing the necessary training and resources to help employees adapt to new methods.
Ensuring Employee Engagement and Motivation
Maintaining a high level of employee engagement is crucial for continual improvement. Strategies to keep employees motivated include:
- Recognition: Acknowledging and rewarding contributions to improvement efforts.
- Career Development: Offering opportunities for professional growth tied to improvement initiatives.
- Empowerment: Allowing employees to make decisions and take action on improvement ideas.
Maintaining Momentum in Improvement Efforts
It's easy for the enthusiasm for improvement to wane over time, especially if results are not immediate. To maintain momentum:
- Set Short-Term Goals: Quick wins can demonstrate the value of improvement efforts and keep the team motivated.
- Regular Reviews: Frequent check-ins can help keep improvement efforts on track and adjust strategies as needed.
- Leadership Support: Continued support from management is vital to sustain improvement initiatives.
By proactively addressing these challenges, organizations can smooth the path for continual improvement and fully realize the benefits of a dynamic and responsive quality management system.
Case Studies and Examples
Understanding Clause 10.3 - Continual Improvement in ISO 9001:2015 can be greatly enhanced by examining real-world applications. Case studies and examples serve as a practical reference to grasp the impact of effective continual improvement processes within organizations.
Success Stories of Continual Improvement
- Manufacturing Excellence: A manufacturing company used Six Sigma methodologies to reduce defects in their production line by 30%, leading to increased customer satisfaction and reduced costs.
- Healthcare Efficiency: A hospital implemented Lean techniques to streamline patient admissions, resulting in shorter wait times and higher patient throughput without compromising care quality.
Lessons Learned from Challenges Faced
- Technology Integration: A tech company struggled with the integration of a new IT system. Through root cause analysis, they identified training gaps and addressed them, which improved system adoption and functionality.
- Supply Chain Disruption: A retailer faced supply chain issues that impacted inventory levels. By employing the PDCA cycle, they optimized their supply chain management, resulting in improved stock availability and reduced holding costs.
Practical Examples of Applying Clause 10.3 in Organizations
- Process Improvement: A service provider utilized customer feedback to re-engineer their service delivery process, reducing service time by 20% and enhancing customer satisfaction scores.
- Employee Engagement: An organization implemented an 'Idea of the Month' program, encouraging employees to submit improvement ideas. This led to several process improvements and increased employee engagement.
These case studies demonstrate the tangible benefits that can be achieved through a commitment to Clause 10.3 - Continual Improvement. They highlight how different sectors can apply the principles of continual improvement to address specific challenges and achieve measurable results.
Continual Improvement and Other ISO Standards
Clause 10.3 - Continual Improvement in ISO 9001:2015 is not an isolated concept but rather a principle that intersects with various other ISO standards. Understanding how continual improvement integrates with these standards can enhance an organization's overall performance and compliance.
Relationship Between ISO 9001:2015 and Other ISO Standards
- ISO 14001 (Environmental Management): Continual improvement in environmental performance requires regular review and enhancement of environmental objectives, similar to quality objectives in ISO 9001.
- ISO 45001 (Occupational Health and Safety): This standard also emphasizes continual improvement in creating safer working conditions, reducing workplace risks, and enhancing health and well-being at work.
- ISO 27001 (Information Security): The iterative process of improving information security management systems aligns with the continual improvement of a QMS, focusing on protecting data integrity, confidentiality, and availability.
Integrating Continual Improvement Across Multiple Standards
Organizations often choose to implement multiple ISO standards simultaneously. To do this effectively:
- Unified Management System: Develop an integrated management system that aligns the common elements of each standard, such as leadership commitment and performance evaluation.
- Consistent Improvement Methodology: Use tools like PDCA and Six Sigma across all standards to maintain a consistent approach to improvement.
- Shared Metrics and Objectives: Where possible, establish KPIs and objectives that serve multiple standards to streamline monitoring and reporting.
By viewing continual improvement as a holistic approach that spans various aspects of organizational performance, businesses can create a more resilient and adaptable management system that delivers enhanced value.
The Future of Continual Improvement
As businesses evolve and new challenges emerge, the concept of continual improvement within the framework of ISO 9001:2015 must also adapt. By anticipating future trends and technological advancements, organizations can stay ahead and ensure their quality management systems remain relevant and effective.
Trends in Quality Management and Continual Improvement
- Data Analytics and Big Data: The use of data analytics tools to analyze large datasets will become increasingly important in identifying trends and improvement opportunities.
- Automation and AI: Artificial intelligence (AI) and automation will play a more significant role in streamlining processes and providing real-time insights for decision-making.
- Sustainability and Social Responsibility: There will be a growing emphasis on improving not just economic performance but also environmental and social impacts.
How Technology is Shaping Continual Improvement Practices
- Predictive Analytics: Organizations will use predictive analytics to anticipate issues before they occur and proactively implement improvements.
- Internet of Things (IoT): Connected devices and IoT will enable more accurate monitoring of processes and performance in real-time, facilitating immediate improvements.
- Collaboration Tools: Advancements in collaboration technology will enhance communication and idea sharing across different locations, fostering a culture of continual improvement.
Predictions for the Evolution of Clause 10.3
- Increased Focus on Agility: Future revisions of ISO 9001 may place greater emphasis on agility and the ability to quickly adapt to changes.
- Integration with Other Management Approaches: There may be a more explicit integration of continual improvement with methodologies like Agile and Scrum, particularly in the software and service industries.
- Broader Impact Measurement: Clause 10.3 may evolve to include a wider range of performance indicators, reflecting the expanding scope of what constitutes value for stakeholders.
The future of continual improvement is dynamic and exciting. Organizations that embrace these trends and remain flexible in their approach will continue to thrive and maintain a competitive edge.
FAQs on Clause 10.3 - Continual Improvement
When delving into the specifics of Clause 10.3 - Continual Improvement in ISO 9001:2015, certain questions frequently arise. Addressing these can help organizations better understand how to implement and benefit from continual improvement practices.
Common Questions About Implementing Clause 10.3
- How often should we review our quality management system for continual improvement?
- Reviews should be conducted at planned intervals to ensure the QMS remains suitable, adequate, and effective, with the frequency depending on the organization's size, complexity, and operational context.
- Can small businesses implement Clause 10.3 effectively?
- Absolutely. While the resources available to small businesses may differ from larger organizations, the principles of continual improvement are scalable and can be adapted to suit any size of operation.
- What is the best way to involve employees in continual improvement?
- Open communication, training, and creating opportunities for employees to contribute to improvement discussions and initiatives are key strategies for involvement.
Best Practices for Sustaining Continual Improvement
- Maintain Clear Documentation: Keep records of improvements, their impacts, and lessons learned to build an institutional memory of continual improvement efforts.
- Regular Training and Education: Provide ongoing training to ensure that all employees understand the importance of continual improvement and the role they play.
- Leadership Involvement: Ensure that top management leads by example and remains visibly committed to continual improvement.
How to Train Staff in Continual Improvement Methodologies
- Workshops and Seminars: Conduct regular training sessions to introduce staff to improvement tools and techniques.
- E-Learning Courses: Utilize online courses that allow employees to learn at their own pace.
- Mentoring and Coaching: Pair less experienced staff with improvement champions who can provide guidance and support.
By addressing these FAQs, organizations can demystify the process of implementing continual improvement and ensure that all employees are aligned with the objectives of Clause 10.3.
Conclusion
Embracing Clause 10.3 - Continual Improvement in ISO 9001:2015 is not just about adhering to a standard; it's about embedding a mindset of perpetual progress within an organization. This clause serves as a reminder that in the journey towards quality excellence, the work is never truly done—there are always new heights to reach and new efficiencies to uncover.
We have explored the multifaceted approach to implementing continual improvement, from understanding its principles to utilizing various tools and techniques, and addressing the inevitable challenges that arise. Through real-world examples, we've seen the transformative power of continual improvement in action, and looked ahead to how it will continue to evolve.
In a world that never stands still, the commitment to continual improvement ensures that organizations can not only keep pace but set the standards for others to follow. It is the cornerstone of a resilient quality management system and a testament to an organization's dedication to never settling for 'good enough.'
As we conclude this comprehensive guide to Clause 10.3 - Continual Improvement, let us not forget that the true measure of success is not in the certifications we hold, but in the relentless pursuit of excellence that propels our organizations forward, day after day.
Next Steps
Are you ready to take your organization's quality management system to the next level? Begin with a thorough assessment of your current processes and see where Clause 10.3 - Continual Improvement can take you. Reach out to us for assistance in ISO 9001 compliance.