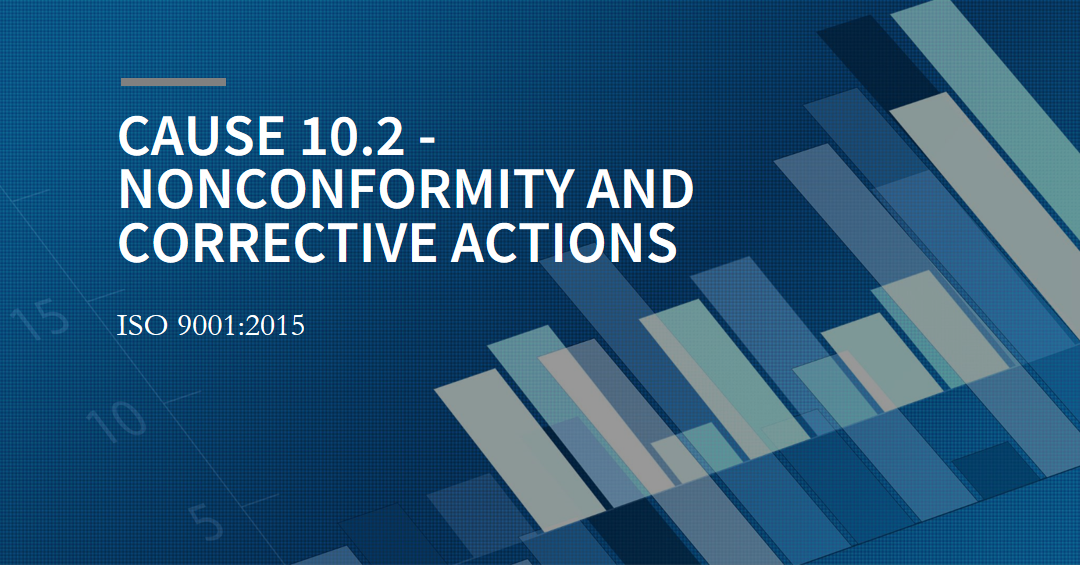
What is Nonconformity in ISO 9001?
Definition of Nonconformity
Nonconformity in the context of ISO 9001 is a breach of the standard's requirements. It occurs when a process, product, or service fails to meet specified criteria, potentially impacting customer satisfaction or the performance of the quality management system.
Types of Nonconformity
There are generally two primary types of nonconformity:
- Process Nonconformity: This occurs when a part of the QMS does not follow the planned arrangements set by the organization's own procedures or the requirements of the ISO 9001 standard.
- Product Nonconformity: This type arises when a product or service fails to meet the specified requirements or customer expectations.
Each type of nonconformity can have a range of implications for a business, from minor issues that are easily corrected to significant problems that may require a robust response.
Examples of Nonconformity in Different Industries
- In manufacturing, a product might fail to meet safety standards.
- In software development, a bug might cause a program to deviate from its intended functionality.
- In healthcare, a patient record might be improperly updated, leading to potential risks in patient care.
The Impact of Nonconformity on Business Operations
Nonconformities can have wide-ranging impacts on a business, including:
- Customer Dissatisfaction: Failing to meet customer requirements can lead to complaints or loss of business.
- Operational Disruption: Nonconformities might cause delays or inefficiencies in production or service delivery.
- Financial Losses: Addressing nonconformities can incur costs, and severe issues may lead to fines or legal action.
By understanding the nature of nonconformity, businesses can better prepare to address issues proactively and maintain compliance with ISO 9001 standards.
In the next section, we will explore Clause 10.2 in detail and understand its objectives and requirements within the QMS framework.
Clause 10.2 – An Overview
The Objectives of Clause 10.2
The primary objective of ISO 9001 Clause 10.2 is to ensure that when nonconformities occur, they are addressed promptly and systematically to prevent recurrence. The clause aims to:
- Maintain the integrity of the quality management system.
- Enhance customer satisfaction by meeting customer requirements consistently.
- Foster a culture of continuous improvement within the organization.
Understanding the Requirements of Clause 10.2
Clause 10.2 sets out the requirements for dealing with nonconformity and taking corrective action. It necessitates that an organization:
- Reacts to the nonconformity and, as applicable, takes action to control and correct it.
- Deals with the consequences of the nonconformity.
- Evaluates the need for action to eliminate the cause(s) of the nonconformity, to prevent recurrence.
- Implements any action needed.
- Reviews the effectiveness of any corrective action taken.
- Updates risks and opportunities determined during planning, if necessary.
- Makes changes to the quality management system, if necessary.
The Importance of Documenting Nonconformities
Documentation is a critical component of Clause 10.2. It serves several important functions:
- Traceability: Provides a record of what happened, when, and who was involved.
- Accountability: Ensures that responsible parties are identified and actions are tracked.
- Analysis: Helps in identifying trends and areas for improvement.
- Evidence of Compliance: Serves as proof that the organization is actively managing its QMS.
Documentation should include:
- The nature of the nonconformity.
- The actions taken to address it.
- The results of corrective actions.
- Any changes made to the quality management system as a result.
By meticulously following Clause 10.2, organizations can turn nonconformities into opportunities for improvement, enhancing the overall effectiveness of their QMS.
Next, we will discuss the corrective action process and provide a step-by-step approach to manage nonconformities effectively.
The Corrective Action Process
Corrective action is a process used to identify, eliminate, and prevent the recurrence of nonconformities in a quality management system. It is a reactive process that kicks in after a nonconformity has been detected. The following steps outline the process for managing corrective actions in accordance with ISO 9001 Clause 10.2.
Steps to Identify Nonconformities
- Monitoring and Measurement: Regular monitoring and measurement of processes, products, and services are crucial for early detection of nonconformities.
- For example, in a manufacturing setting, this may involve routine inspections and quality checks of products against established standards.
- Evaluation of Data: Analyzing data from monitoring activities helps pinpoint areas where nonconformities arise.
- For example, trend analysis of customer feedback may reveal recurring issues with a specific product feature.
Investigating the Cause of Nonconformities
- Root Cause Analysis Techniques: To prevent recurrence, it is essential to understand the root cause of a nonconformity.
- Techniques such as the "5 Whys", Fishbone Diagrams, and Pareto Analysis can be employed to drill down to the underlying issues.
Determining and Implementing Corrective Actions
- Action Plan Development: Once the cause is identified, an action plan is developed to address it. This plan should outline the steps needed, resources required, and timelines for implementation.
- For example, if a nonconformity is due to inadequate training, the action plan may include developing a new training program for employees.
- Resource Allocation for Corrective Actions: Assigning the necessary resources, both human and material, to implement the corrective actions is vital for effectiveness.
- For instance, allocating budget for new equipment or additional staff to manage increased quality control measures.
Reviewing the Effectiveness of Corrective Actions
After implementing corrective actions, it's important to review their effectiveness. This involves monitoring the outcomes to ensure that the nonconformity has been resolved and is not likely to recur.
Documenting and Recording the Corrective Action Process
Throughout the corrective action process, documentation is key. Records should be kept of:
- The nature and details of the nonconformity.
- The investigation process and findings.
- The corrective action plan, including responsibilities and timelines.
- The results of the corrective action and any follow-up measures.
By rigorously following these steps, organizations can not only address nonconformities when they arise but also bolster their processes against future issues, fostering a resilient and continuously improving quality management system.
In the next section, we will explore best practices for managing nonconformity and corrective actions to ensure a robust and effective QMS.
Best Practices for Managing Nonconformity and Corrective Actions
Adopting best practices for managing nonconformity and corrective actions is not only essential for compliance with ISO 9001 Clause 10.2 but also for the overall health of an organization's quality management system. Here are some key strategies to ensure effective management of nonconformities and corrective actions.
Implementing a Proactive Approach to Nonconformity
- Predictive Analysis: Use data analytics to predict where nonconformities might occur and take preemptive actions.
- Preventive Maintenance: Regularly service equipment and update software to prevent malfunctions that could lead to nonconformities.
Fostering a Culture of Quality and Continuous Improvement
- Employee Empowerment: Encourage employees to identify potential issues and suggest improvements.
- Quality Training: Provide ongoing training to ensure that all employees understand the importance of quality and their role in maintaining it.
Training and Awareness for Staff on Clause 10.2
- Regular Workshops: Conduct workshops to keep staff informed about the processes involved in Clause 10.2.
- Clear Communication: Ensure that the steps for handling nonconformities and corrective actions are clearly communicated and accessible to all employees.
Utilizing Technology for Tracking Nonconformities and Corrective Actions
- Quality Management Software: Implement software that can track nonconformities, corrective actions, and their outcomes over time.
- Automated Alerts: Set up automated alerts to notify relevant personnel when a nonconformity is detected or when corrective actions are due for review.
By integrating these best practices into the day-to-day operations, organizations can create a strong foundation for quality management, ensuring that nonconformities are handled effectively and efficiently.
The following section will address common pitfalls to avoid when dealing with ISO 9001 Clause 10.2.
Common Mistakes to Avoid with ISO 9001 Clause 10.2
Successfully managing nonconformities and corrective actions is critical for maintaining a robust Quality Management System. However, even the best-intentioned organizations can fall into traps that hinder their compliance with ISO 9001 Clause 10.2. Here are some common mistakes to watch out for:
Inadequate Root Cause Analysis
- Superficial Investigation: Corrective actions can fail if the investigation does not go deep enough to uncover the true root cause of the nonconformity.
- Ignoring Systemic Issues: Focusing solely on the immediate cause without considering broader systemic issues can lead to repeated nonconformities.
Overlooking the Importance of Employee Involvement
- Lack of Engagement: Failure to involve employees who are directly affected by the nonconformity can result in ineffective corrective actions.
- Insufficient Training: Employees must be adequately trained to identify and manage nonconformities.
Insufficient Documentation and Record-Keeping
- Inaccurate Records: Incomplete or inaccurate documentation can obscure the nonconformity's history and impede the effectiveness of corrective actions.
- Record Accessibility: All relevant personnel should have easy access to nonconformity and corrective action records.
Failure to Review Corrective Actions' Effectiveness
- Neglecting Follow-up: Without reviewing the results of corrective actions, organizations won't know if the nonconformity could recur.
- Ignoring Feedback: Employee and customer feedback is valuable for assessing the success of corrective actions.
By being aware of these common mistakes, organizations can take proactive steps to avoid them, ensuring a more effective and compliant approach to managing nonconformities and corrective actions under ISO 9001 Clause 10.2.
Next, we'll explore the role of leadership in ensuring compliance with Clause 10.2 and fostering an environment that supports quality management.
The Role of Leadership in Clause 10.2 Compliance
The involvement of leadership is paramount in ensuring the success of a Quality Management System, particularly when it comes to Clause 10.2 – Nonconformity and Corrective Actions. The commitment and actions of top management can greatly influence how effectively an organization addresses nonconformities and implements corrective measures.
Leadership Commitment to Quality Management
- Setting the Tone: Leaders must demonstrate their commitment to quality through clear communication and participation in quality initiatives.
- Providing Resources: It is the leadership's responsibility to ensure that adequate resources are available for corrective actions to be effective.
The Role of Top Management in Corrective Actions
- Active Involvement: Leaders should be actively involved in the corrective action process, from initiation to review of effectiveness.
- Decision Making: Top management plays a critical role in making decisions related to significant nonconformities and the actions required to address them.
Strategies for Leadership to Support Clause 10.2 Processes
- Visibility: Leaders should maintain a visible presence in quality management activities to reinforce their importance.
- Recognition: Acknowledging and rewarding the successful management of nonconformities can motivate staff to maintain high quality standards.
- Continuous Learning: Encouraging a culture of continuous learning and improvement among all levels of the organization helps to prevent future nonconformities.
The leadership's role in Clause 10.2 compliance cannot be overstated. Their actions set a precedent for the entire organization, influencing the effectiveness of the QMS and the continuous improvement of processes.
Moving forward, we will discuss the auditing process for compliance with Clause 10.2 and what organizations can expect during an audit.
Auditing for Compliance with Clause 10.2
Auditing is a critical element of the ISO 9001 framework, providing an objective assessment of whether an organization's Quality Management System meets the requirements of the standard, including those related to nonconformity and corrective actions. Here's how to prepare for and what to expect during an audit for Clause 10.2 compliance.
Preparing for an ISO 9001 Clause 10.2 Audit
- Documentation Review: Ensure that all records of nonconformities and corrective actions are up-to-date and readily available.
- Employee Briefing: Staff should be aware of the audit process and their roles in it. They should understand the procedures for identifying, reporting, and addressing nonconformities.
- Mock Audits: Conducting internal audits can help identify gaps in the QMS before the external audit takes place.
What Auditors Look For in Clause 10.2 Compliance
Auditors will typically review the following:
- Nonconformity Records: Evidence that nonconformities are being identified, documented, and addressed in a timely manner.
- Corrective Action Documentation: Documentation that demonstrates the steps taken to correct nonconformities and prevent their recurrence.
- Effectiveness of Actions: Proof that corrective actions have been effective in eliminating the root causes of nonconformities.
- Continual Improvement: Indications that the organization is using the outcomes of corrective actions for continual improvement.
Responding to Audit Findings Related to Nonconformity and Corrective Actions
- Immediate Action: If the audit reveals any nonconformities, it's important to address them as quickly as possible.
- Long-Term Solutions: Develop a plan for long-term corrective actions to prevent recurrence of the identified nonconformities.
- Communication with Auditors: Maintain open lines of communication with auditors to understand their concerns and the rationale behind their findings.
By thoroughly preparing for an audit and understanding what auditors look for in Clause 10.2 compliance, organizations can better position themselves to meet ISO 9001 standards and demonstrate their commitment to quality management.
In the next section, we will explore how Clause 10.2 integrates with other clauses of ISO 9001 and the synergies that can be leveraged.
Integrating Clause 10.2 with Other ISO 9001 Clauses
Understanding the interrelationship between Clause 10.2 and other clauses of ISO 9001 is crucial for developing a holistic Quality Management System (QMS). Here's how Clause 10.2 aligns with and supports other key clauses of the standard.
Connection with Clause 4 – Context of the Organization
- Alignment with Organizational Goals: Nonconformity and corrective action processes should be aligned with the broader business objectives and context.
- Stakeholder Expectations: Understanding the needs and expectations of relevant stakeholders is essential when addressing nonconformities and implementing corrective actions.
Synergy with Clause 6 – Planning
- Risk-Based Thinking: Clause 10.2's emphasis on corrective actions complements the risk-based approach to planning, allowing for preemptive measures and mitigation strategies.
- Objectives and Planning to Achieve Them: The corrective action process should contribute to achieving quality objectives set out in the planning phase.
Interactions with Clause 9 – Performance Evaluation
- Monitoring and Measurement: The evaluation of the effectiveness of corrective actions relies on the monitoring and measurement strategies outlined in Clause 9.
- Internal Audit: The internal audit process is a key component of performance evaluation, providing insights into the effectiveness of the nonconformity and corrective action processes.
By integrating Clause 10.2 effectively with other clauses of ISO 9001, organizations can ensure a consistent and comprehensive approach to quality management, where each part of the QMS supports and enhances the others.
We will now look at some case studies that illustrate the successful implementation of corrective actions and the lessons learned from nonconformity issues.
Case Studies
Case studies provide valuable insights into the practical application of ISO 9001 Clause 10.2 in various organizational contexts. They offer real-world examples of how businesses have successfully addressed nonconformities and implemented corrective actions. Here are a couple of instances that highlight the importance of an effective approach to managing nonconformity and corrective actions.
Successful Implementation of Corrective Actions
Case Study 1: Manufacturing Sector
- Background: A car manufacturer identified a recurring nonconformity in the paint finish on its vehicles.
- Corrective Actions: The company conducted a root cause analysis and discovered that a faulty spray gun was causing the issue. The corrective action involved replacing the defective equipment and retraining staff on equipment maintenance protocols.
- Results: After implementing these actions, the company saw a significant decrease in paint-related defects, leading to improved customer satisfaction and reduced rework costs.
Case Study 2: Service Industry
- Background: A software development firm frequently missed project deadlines, leading to client dissatisfaction.
- Corrective Actions: The firm analyzed project management processes and found that poor communication was a contributing factor. A new project management tool was introduced to facilitate better communication among team members.
- Results: The introduction of the new tool, along with additional training on its use, resulted in more efficient project timelines and enhanced client trust.
Lessons Learned from Nonconformity Issues
Case Study 3: Healthcare Sector
- Situation: A hospital faced issues with incorrect patient medication records, a critical nonconformity in patient care.
- Lesson: The investigation revealed that the electronic health record system was not user-friendly, leading to input errors. The hospital learned the importance of involving end-users in the selection and implementation of such systems to ensure they meet the users' needs effectively.
Case Study 4: Food Industry
- Situation: A food processing company encountered a nonconformity with food safety standards due to cross-contamination.
- Lesson: The corrective action included redesigning the layout of the processing area to prevent cross-contamination and implementing stricter hygiene protocols. The lesson learned was that sometimes, process and environmental changes are necessary to address nonconformities fully.
These case studies demonstrate that with a diligent approach to identifying, addressing, and preventing nonconformities, organizations can not only comply with ISO 9001 Clause 10.2 but also drive significant improvements in their quality management processes.
In the conclusion, we will summarize the importance of ISO 9001 Clause 10.2 and the ongoing process of quality improvement.
Conclusion
ISO 9001 Clause 10.2 is not just a requirement for compliance; it's a pivotal part of an organization's journey towards excellence in quality management. By effectively managing nonconformity and corrective actions, businesses are able to turn challenges into opportunities for improvement, thereby enhancing their operations, customer satisfaction, and overall success.
Key Takeaways:
- Proactive Mindset: Viewing nonconformities as chances for improvement rather than setbacks can lead to stronger processes and a more resilient QMS.
- Systematic Approach: A structured and methodical approach to corrective actions ensures that nonconformities are addressed thoroughly and recurrence is prevented.
- Leadership Involvement: Top management's commitment to quality and active participation in the corrective action process is essential for fostering a culture of quality.
- Continual Improvement: The cycle of planning, implementing, reviewing, and improving is at the heart of ISO 9001, and Clause 10.2 is a critical component of this cycle.
Remember, the process of managing nonconformities is continuous. It requires vigilance, dedication, and a willingness to learn and adapt. By embracing the principles of Clause 10.2, organizations can not only achieve compliance with ISO 9001 but also drive meaningful, long-term improvements that benefit all stakeholders.
This post has aimed to provide a comprehensive understanding of ISO 9001 Clause 10.2. We welcome your questions and are here to support your journey toward mastering nonconformity and corrective actions.
Frequently Asked Questions (FAQs)
What is the difference between correction and corrective action in ISO 9001?Correction refers to the immediate actions taken to fix a detected nonconformity, while corrective action is a process aiming to eliminate the root causes of the nonconformity to prevent recurrence.
How often should nonconformity and corrective action processes be reviewed?These processes should be reviewed regularly, as part of the internal audit cycle, and whenever there are changes in operations or when a nonconformity occurs.
Can a business still be ISO 9001 certified if nonconformities occur?Yes, as long as the nonconformities are properly documented, addressed, and corrective actions are implemented to prevent their recurrence, a business can maintain its ISO 9001 certification.
How long should records of nonconformities and corrective actions be retained?Records should be retained according to the organization's documented information retention policy and any applicable legal or regulatory requirements.
Resources and Further Reading
For more in-depth knowledge on ISO 9001 Clause 10.2 and quality management systems, the following resources are recommended: