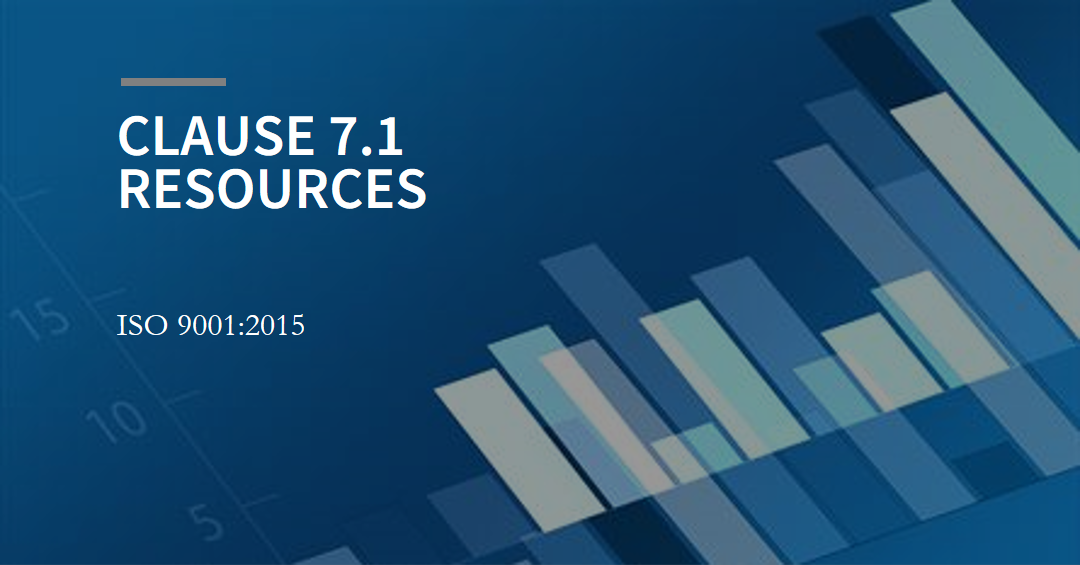
Introduction to ISO 9001:2015 and Resource Management
In the realm of Quality Management Systems (QMS), ISO 9001:2015 stands as a pivotal standard, guiding organizations in establishing processes that consistently meet customer and regulatory requirements. A critical component of this standard is Clause 7.1 – Managing Resources, which lays the foundation for ensuring the necessary resources are available to establish, implement, maintain, and continually improve the QMS.
The significance of effective resource management cannot be overstated. It is the lifeblood that fuels all aspects of an organization, from its human capital to its technological assets. Effective resource management is not just about having enough resources; it's about optimizing their use to achieve the strategic objectives of the business. This optimization ensures that resources contribute to the QMS's efficiency and effectiveness, ultimately leading to improved customer satisfaction and business performance.
Clause 7.1 of ISO 9001:2015 articulates the requirements for organizations to control and manage resources adequately. This includes considerations for people, infrastructure, environment, monitoring and measuring resources, and organizational knowledge. Each sub-clause provides a framework for understanding and implementing resource management practices that align with quality objectives.
In this comprehensive guide, we will delve into the depths of Clause 7.1, providing a detailed analysis of its components, practical insights for implementation, and the impact of managing resources on ISO 9001:2015 compliance. By the end of this post, you will have a thorough understanding of how to harness the full potential of Clause 7.1 to strengthen your QMS and drive business excellence.
Let's embark on this journey to master the art of managing resources in ISO 9001:2015, ensuring your organization has the tools and knowledge to thrive in today's competitive landscape.
Breakdown of Clause 7.1 – Managing Resources in ISO 9001:2015
Delving into the specifics of Clause 7.1 – Managing Resources, we discover a comprehensive approach to ensuring that an organization can consistently meet customer and regulatory requirements through optimal resource allocation. Let's dissect this clause and its key components to understand better the breadth and depth of its implications for a Quality Management System.
What Does Clause 7.1 Entail?
Clause 7.1 encompasses various aspects of resource management, each critical to the success of a QMS. It requires organizations to determine and provide the resources needed for the establishment, implementation, maintenance, and continual improvement of the QMS.
Key Components of Clause 7.1
The clause is divided into several sub-clauses, each addressing a different resource type that must be managed effectively:
- General requirements: Organizations must consider current and future needs, including human resources, infrastructure, and the environment necessary for operation.
- People (7.1.2): The competence, awareness, and adequate number of personnel are vital.
- Infrastructure (7.1.3): The physical and technological structures necessary for operations must be maintained.
- Environment for the operation of processes (7.1.4): The work environment should support the operation of processes.
- Monitoring and measuring resources (7.1.5): Appropriate resources must be available for accurate and consistent monitoring and measuring.
- Organizational knowledge (7.1.6): Necessary knowledge must be maintained, protected, and made available where needed.
Understanding the Terminology Used in Clause 7.1
To fully grasp Clause 7.1, it is essential to understand the terms used within the context of ISO 9001:2015:
- Infrastructure refers to the buildings, workspace, hardware, software, and transportation resources that an organization utilizes.
- Environment for operation of processes encompasses conditions under which work is performed, including physical, social, psychological, and environmental factors.
- Monitoring and measuring resources are the tools and devices used to verify that products and services meet requirements.
- Organizational knowledge is the cumulative information and experience that an organization has, which is necessary for achieving conformity of products and services.
By comprehensively managing these components, organizations can ensure that their QMS is robust, resilient, and responsive to the ever-changing business landscape.
In the following sections, we will explore each sub-clause of Clause 7.1 in further detail, providing actionable insights and strategies for effective implementation within your QMS.
People: The Core of Organizational Resources (7.1.2)
At the heart of every successful organization lie its people. Clause 7.1.2 of ISO 9001:2015 recognizes the critical role that human resources play in the quality management process. Here, we delve into how people are fundamental to the QMS and what organizations must do to harness their potential.
The Role of Human Resources in ISO 9001:2015
Human resources are not merely a pool of labor; they are the carriers of expertise, innovation, and the driving force behind every process within the QMS. The standard emphasizes the need for competent staff who are aware of their contribution to the effectiveness of the QMS, including the benefits of improved performance.
Identifying and Providing Necessary Competencies
Organizations must:
- Determine the necessary competence for personnel performing work that affects product and service quality.
- Ensure that these persons are competent based on education, training, or experience.
- Take actions to acquire the necessary competence, and evaluate the effectiveness of these actions.
- Maintain documented information as evidence of competence.
For example, a company may implement a skills matrix to map out required competencies for specific roles and use it to identify training needs and performance evaluations.
Ensuring Staff Awareness and Their Role in QMS
Staff must be made aware of:
- The quality policy.
- Relevant quality objectives.
- Their contribution to the effectiveness of the QMS, including the benefits of improved performance.
- The implications of not conforming with the QMS requirements.
This awareness can be fostered through regular training sessions, workshops, and internal communication strategies that keep quality management principles at the forefront of employees' daily activities.
Case Study: Enhancing Human Resources for Quality Excellence
A manufacturing company faced frequent non-conformities in its production processes. After analyzing the root causes, it was discovered that a lack of training and awareness among the floor staff was a significant contributor to the issue. The company responded by designing a comprehensive training program focused on quality standards, operational procedures, and the importance of each employee's role in the QMS. Post-training evaluations showed a marked decrease in non-conformities and an increase in overall product quality.
By investing in its people, the organization not only improved its compliance with ISO 9001:2015 but also boosted employee morale and customer satisfaction.
Human resources are not just a part of the organization; they are the essence of its capability to deliver quality. Managing human resources effectively means aligning their growth and development with the strategic direction of the QMS, leading to sustained success.
Infrastructure: Building a Supportive Environment (7.1.3)
Infrastructure is more than the physical space where an organization operates; it's the backbone that supports the entire workflow and processes necessary to achieve quality objectives. Clause 7.1.3 of ISO 9001:2015 outlines the requirements for establishing, maintaining, and continually improving the infrastructure needed to achieve conformity of products and services.
Physical and Technological Infrastructure Requirements
Organizations must consider various aspects of their physical and technological infrastructure:
- Buildings, workspace, and associated utilities
- Equipment, including hardware and software
- Transportation resources
- Information and communication technology
For instance, a software development company must ensure that its IT infrastructure can handle the development, testing, and deployment of software efficiently and securely.
Maintenance of Infrastructure to Support Operations and QMS
Regular maintenance and updates of the infrastructure are crucial to prevent breakdowns and ensure smooth operation. This includes:
- Scheduled maintenance and timely repairs of equipment
- Upgrades to software and hardware to keep up with technological advances
- Ensuring the workspace is conducive to productivity and employee well-being
Case Study: Infrastructure Optimization for Quality Improvement
A logistics company, after experiencing delays in order processing and inventory discrepancies, conducted an audit of its infrastructure. It was discovered that outdated warehouse management software and inefficient storage facilities were the root causes. By investing in state-of-the-art software and reorganizing the warehouse layout, the company significantly reduced processing times and improved inventory accuracy.
This case illustrates the direct impact that infrastructure can have on the quality of products and services and the importance of its continuous improvement.
To summarize, infrastructure is a critical element of the resource management system outlined in Clause 7.1.3. When managed effectively, it provides a solid platform from which all organizational activities can operate efficiently, reliably, and to a high-quality standard.
Optimizing the Work Environment (7.1.4)
Creating a conducive work environment is essential for facilitating efficient and effective operations. Clause 7.1.4 of ISO 9001:2015 focuses on the establishment, maintenance, and continuous improvement of the environment necessary for the operation of processes. This environment directly influences the quality of output and the performance of the QMS.
Factors that Influence the Work Environment
The work environment encompasses a variety of elements that can affect the performance of work activities, including:
- Physical conditions such as lighting, temperature, and noise levels
- Ergonomic requirements like workspace design and comfort
- Psychological aspects including stress levels, workload management, and interpersonal relationships
- Safety conditions ensuring the well-being of employees
Organizations should conduct regular assessments to identify and mitigate any factors that could negatively impact the work environment.
Aligning the Work Environment with Quality Objectives
To optimize the work environment, organizations should:
- Align environmental factors with the needs of personnel and the requirements of work processes.
- Implement controls to manage identified risks and enhance positive influences.
- Continuously monitor the effectiveness of these controls and make necessary adjustments.
For example, a production company might find that excessive noise on the plant floor is causing communication issues and errors. By installing sound-dampening materials and providing noise-cancellation headphones, the company could see a reduction in mistakes and improvements in employee satisfaction.
Case Study: Work Environment Enhancement Leads to Increased Productivity
A tech startup was struggling with low employee morale and high turnover rates. Upon evaluating their work environment, they realized that the lack of collaborative spaces and rigid work schedules were contributing factors. By redesigning the office layout to include more open and communal areas and introducing flexible work hours, the startup saw a significant boost in team collaboration and a decrease in turnover, leading to a more productive and engaged workforce.
This case study emphasizes the importance of aligning the work environment with the needs of the workforce and the goals of the organization to achieve optimal results.
In essence, the work environment is a critical component of the resource management system that can significantly impact the effectiveness of the QMS and the quality of the products and services provided. By understanding and managing the various factors that contribute to the work environment, organizations can create a setting that supports their quality objectives and enhances overall performance.
Monitoring and Measuring Resources (7.1.5)
In the world of quality management, the adage "you can't manage what you can't measure" holds true. Clause 7.1.5 of ISO 9001:2015 underlines the need for appropriate monitoring and measuring resources, which are indispensable for an organization to ensure conformity and enhance the quality of products and services.
Importance of Monitoring and Measuring for Quality Control
Organizations must:
- Determine the need for monitoring and measuring to provide evidence of conformity with determined quality requirements.
- Ensure that valid and reliable monitoring and measuring results are obtained when these processes are performed.
- Establish a systematic approach to monitor the effectiveness of their QMS.
Types of Monitoring and Measuring Equipment Needed
Depending on the nature of the business, the following resources might be necessary:
- Precision instruments for manufacturing industries to measure product dimensions
- Software tools for service industries to track project milestones and customer satisfaction
- Analytical equipment for laboratories to ensure the quality of chemical substances
Calibration and Verification of Monitoring and Measuring Resources
To maintain trust in the accuracy of measurements, organizations must:
- Calibrate or verify monitoring and measuring equipment at specified intervals or prior to use.
- Adjust the equipment if found to be out of calibration to ensure accurate results.
- Identify the equipment with a suitable indicator or record to determine its calibration status.
- Maintain documented information as evidence of the fitness for purpose of monitoring and measuring resources.
For example, a food processing company might implement a schedule for the regular calibration of temperature sensors to ensure that products are stored and processed in safe conditions, thus maintaining product quality and safety.
Case Study: Precision in Aerospace Component Manufacturing
An aerospace component manufacturer had stringent requirements for part precision. They noticed inconsistencies in measurements that led to non-conformities. Upon investigation, it was discovered that their measuring instruments were not regularly calibrated. The company instituted a rigorous calibration program, which dramatically reduced measurement discrepancies and improved the quality of their components.
This example demonstrates the impact that effectively managed monitoring and measuring resources can have on an organization's ability to deliver high-quality products and services.
Monitoring and measuring resources are vital for any organization looking to deliver on its promise of quality. By effectively managing these resources, an organization can ensure the accuracy of its measurements and, consequently, the quality of its output. This attention to detail not only fulfills the requirements of Clause 7.1.5 but also builds a foundation of trust with customers and stakeholders.
Organizational Knowledge: Preserving and Sharing Information (7.1.6)
The sustainability and growth of an organization are greatly influenced by how it manages its knowledge base. Clause 7.1.6 of ISO 9001:2015 highlights the importance of organizational knowledge as a resource that needs to be captured, maintained, and disseminated effectively to achieve and maintain a high level of quality in products and services.
Defining and Managing Organizational Knowledge
Organizational knowledge encompasses the collective information, experience, and expertise of an organization. It includes:
- Intellectual property
- Lessons learned from experience
- Insights gained from data analysis
- Knowledge contained within standards, manuals, and processes
Organizations are required to determine the knowledge necessary for the operation of processes and to achieve conformity of products and services. This knowledge must be maintained and be made available to the extent necessary. Additionally, organizations need to address the need to acquire new knowledge and ensure it is integrated into the QMS.
Strategies for Maintaining and Improving Knowledge Resources
Effective knowledge management can be achieved through:
- Documenting important processes and procedures
- Implementing training programs that facilitate knowledge transfer
- Encouraging a culture of continuous learning and improvement
- Utilizing technology to store and share knowledge, such as intranets or knowledge management systems
For instance, a consulting firm could create a centralized database that captures project experiences, best practices, and client feedback, which can then be used to train new employees and refine existing methodologies.
Case Study: Knowledge Management in Pharmaceutical R&D
A pharmaceutical company faced challenges in preserving the specialized knowledge of its R&D team. To address this, they implemented a knowledge retention program that included mentorship schemes, detailed documentation of research protocols, and collaborative tools for sharing insights across departments. As a result, the company was able to maintain a high level of innovation and quality in its drug development process, even when key team members left the organization.
This case study underscores the value of organizational knowledge and how proactive management of this resource can contribute to the sustained success of a company.
Organizational knowledge is a strategic asset that needs careful management. By adhering to the requirements of Clause 7.1.6, organizations can ensure they possess the necessary knowledge to support the operation of their processes and the achievement of conformity in their products and services. This not only contributes to the effectiveness of the QMS but also enhances the organization's overall capability to compete in the market.
Implementing Clause 7.1 in Your QMS
Implementing Clause 7.1 – Managing Resources within your Quality Management System (QMS) is a strategic endeavor that enhances the overall effectiveness and efficiency of your organization. This implementation involves a systematic approach to assess, plan, and integrate resource management into your QMS processes.
Steps for Assessing Current Resource Management Practices
To effectively implement Clause 7.1, organizations should:
- Conduct a Gap Analysis: Review current resource management practices against ISO 9001:2015 requirements to identify areas for improvement.
- Engage Stakeholders: Involve personnel from different levels and functions to understand resource needs and expectations.
- Document Resource Requirements: Establish documented information outlining the resources required for each process and how they contribute to product and service conformity.
Planning and Implementing Resource Management Improvements
Once the assessment is complete, organizations can:
- Develop a Resource Management Plan: Outline actions, timelines, and responsibilities for addressing identified gaps and improving resource management.
- Allocate Budget and Resources: Ensure that adequate resources, including finances and personnel, are allocated for the implementation of the plan.
- Monitor Implementation Progress: Set up monitoring mechanisms to track the progress of implementation and make necessary adjustments.
Integrating Clause 7.1 Requirements into Existing Processes
Integration into existing processes may involve:
- Updating Policies and Procedures: Amend existing policies and procedures to include resource management requirements.
- Enhancing Training Programs: Provide training to staff on the importance of resource management and their roles in it.
- Leveraging Technology: Utilize technology solutions, such as Enterprise Resource Planning (ERP) systems, to streamline resource allocation and monitoring.
Case Study: Implementing Resource Management in a Service Organization
A financial services firm sought to improve its resource management to enhance customer satisfaction and operational efficiency. The firm conducted a comprehensive assessment and developed a resource management plan that included upgrading its IT infrastructure, implementing a new training program for customer service representatives, and redesigning its office layout to create a more collaborative environment. As a result, the firm experienced a significant increase in customer satisfaction scores and a reduction in service delivery times.
By following a structured approach to implementing Clause 7.1, organizations can ensure that they have the right resources in place to support their QMS and achieve their quality objectives.
Challenges and Best Practices in Resource Management
Resource management within the context of ISO 9001:2015 can present various challenges. However, by understanding these challenges and employing best practices, organizations can navigate them successfully and enhance their QMS.
Common Obstacles in Managing Resources According to ISO 9001:2015
Some of the challenges organizations might face include:
- Limited Budgets: Financial constraints can hinder the ability to allocate sufficient resources.
- Changing Technology: Keeping up with rapid technological advancements can be difficult.
- Employee Resistance: Implementing new processes or technologies may meet with resistance from staff.
- Resource Allocation: Deciding how best to allocate resources efficiently to different areas of the organization.
Best Practices for Effective Resource Management
To overcome these challenges, consider the following best practices:
- Prioritize Resource Needs: Clearly define and prioritize resource needs based on their impact on quality objectives.
- Engage Employees: Involve employees in decision-making processes related to resource management to increase buy-in and reduce resistance.
- Continuous Training: Invest in continuous training and development to keep up with technological changes and enhance employee competencies.
- Leverage Partnerships: Form strategic partnerships to gain access to additional resources or specialized expertise.
Case Studies: Successful Implementation of Clause 7.1
- Technology Upgrade in Manufacturing: A manufacturing company facing outdated equipment challenges implemented a technology upgrade plan, prioritizing machinery that directly impacted product quality. By leasing equipment rather than purchasing, they managed costs while improving quality.
- Employee Engagement in Healthcare: A healthcare provider struggling with staff resistance to new procedures introduced an employee engagement program that included regular town hall meetings and suggestion boxes. This led to increased staff participation and smoother implementation of new resource management practices.
By employing these best practices and learning from others' experiences, organizations can effectively manage their resources and support their QMS.
Monitoring, Evaluation, and Continual Improvement
The dynamic nature of business necessitates a vigilant approach to resource management. Monitoring, evaluation, and continual improvement are integral to ensuring that the resources allocated to the QMS remain effective over time. ISO 9001:2015 encourages a cycle of ongoing assessment and enhancement to maintain a high-performance QMS.
Setting up Processes for Regular Monitoring of Resources
To stay on top of resource management, organizations should:
- Develop Key Performance Indicators (KPIs): Identify KPIs related to resource utilization and quality outcomes.
- Implement Regular Audits: Schedule and conduct regular audits to assess the efficiency and effectiveness of resource use.
- Gather and Analyze Data: Collect data on resource performance and analyze it to identify trends and areas for improvement.
Techniques for Evaluating Resource Management Effectiveness
Evaluation can include:
- Benchmarking Against Best Practices: Compare resource management practices against industry standards or competitors.
- Feedback Mechanisms: Use surveys, interviews, and feedback forms to gather insights from employees and customers.
- Cost-Benefit Analysis: Evaluate the financial impact of resource management decisions on the organization's bottom line.
Continual Improvement Practices for Resource Management
To foster continual improvement, organizations can:
- Implement Corrective Actions: When issues are identified, develop and implement corrective actions to address them.
- Encourage Innovation: Create an environment that encourages employees to propose innovative solutions for resource management.
- Review and Update Resource Plans: Regularly review resource management plans to ensure they remain aligned with organizational goals and make updates as necessary.
Case Study: Continual Improvement in a Tech Company
A software development company experienced a plateau in productivity despite having abundant resources. They instituted a continual improvement program that involved regular team retrospectives to discuss challenges and successes. By analyzing performance data and gathering team feedback, they identified that the allocation of development resources was misaligned with project demands. The company adjusted its resource allocation model, resulting in a 15% increase in project delivery speed and a higher rate of customer satisfaction.
This case study illustrates the power of monitoring, evaluation, and continual improvement in enhancing the effectiveness of resource management within a QMS.
By embedding these practices into the fabric of the organization, companies can ensure they not only meet the requirements of Clause 7.1 but also drive ongoing advancements in their QMS.
Conclusion
Throughout this comprehensive exploration of Clause 7.1 – Managing Resources in ISO 9001:2015, we've uncovered the multifaceted nature of effective resource management and its critical role in sustaining a robust QMS. From recognizing the pivotal role of human resources to maintaining a conducive work environment, and from ensuring precision in monitoring and measurement to preserving organizational knowledge, we've seen how each component forms a piece of the greater puzzle.
To recap, effective resource management under Clause 7.1 involves:
- Understanding and providing the necessary competencies and awareness for your staff.
- Building and maintaining an infrastructure that supports and enhances operational processes.
- Optimizing the work environment to align with quality objectives and enhance productivity.
- Ensuring the reliability of monitoring and measuring resources through regular calibration and maintenance.
- Preserving and continually improving the organizational knowledge necessary for the conformity of products and services.
By implementing the strategies outlined in this guide, organizations can not only achieve compliance with ISO 9001:2015 but also unlock potential for increased efficiency, improved customer satisfaction, and sustained competitive advantage.
Remember, the journey of managing resources is ongoing. It demands vigilance, adaptability, and a commitment to continual improvement. With these principles at the forefront, organizations can thrive in today's complex and ever-evolving business landscape.